Welcome to the Surface Roughness Analysis Blog
Why do brakes squeak? When will a gasket leak? What caused the haziness in my painted finish?
Surface texture and function are tightly linked. Understanding the relationship between texture and function, and sharing that information with engineers and quality professionals, is what Michigan Metrology is all about.
The articles in this blog explore the concepts of surface texture analysis and measurement. We show how you can apply these concepts to solve problems related to leaks, squeaks, appearance, wear, noise, fit, friction, vibration, adhesion, and many other functions.
Looking for more information on specific surface texture parameters? Visit our Surface Texture Parameters Glossary for an introduction to dozens of 3D surface roughness analysis parameters.
And, if you want to learn much more about surface texture consider attending our online and in-person classes for an immersive introduction to the many concepts in surface analysis.
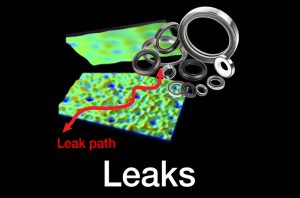
Why do seals leak when the average roughness meets spec?
June 13, 2025Surface texture plays a major role in sealing. But just making a surface “rougher” or “smoother” may not improve how well your surfaces seal. Interested in a deep dive into
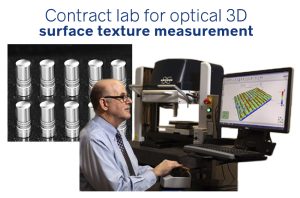
I need 3D surface texture measurement (but a new system isn’t in the budget)
April 22, 2025Measuring surface roughness in 3D can offer a host of benefits. But for many companies, a measurement system may not be in the near-term budget. Here’s a way to reap
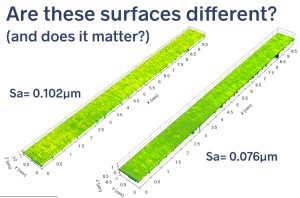
My Ra values are different…should I care?
March 25, 2025The average roughness parameter (Ra, or Sa for 3D measurements) is helpful for spotting changes in a surface or in surface-forming processes. A common question, however, is: how much of
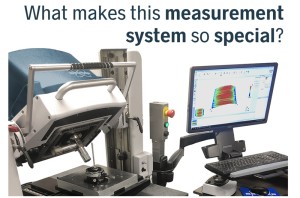
What makes this measurement system so special?
January 2, 2025Through Michigan Metrology’s 30 years in business, we’ve owned many generations of 3D surface texture measurement instruments. For the past 10 years we’ve been lucky to have what we consider
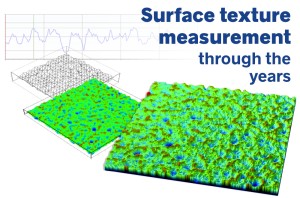
3D surface texture measurement through the years
December 19, 2024As we’re continuing to look back on our 30 years in surface texture measurement, we thought it would be interesting to look at how far measurement technology has come over
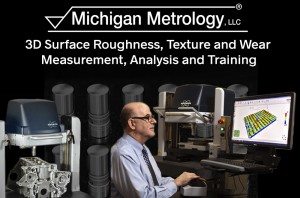
Video Intro to Michigan Metrology
November 8, 2024Don Cohen decribes Michigan Metrology’s contract measurement services, measurement consulting, and surface roughness/wear/tribology training classes. Learn how Michigan Metrology can help you solve issues related to leaks, squeaks, friction, wear,
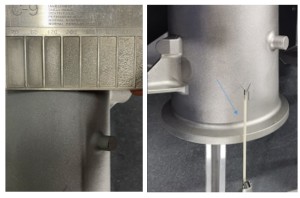
New paper focuses on surface finish for castings
October 17, 2024The surface finish of castings can be as critical to quality as for any precision surface. Yet, finish requirements in the industry are often ill defined, loosely referencing RMS roughness
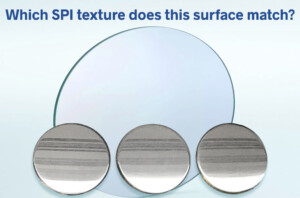
Can you tell these plastic finishes apart?
August 9, 2024Most surface finish specifications for plastics refer to an SPI finish (SPI mold finish). These numbers refer to a standard set of finishes for injection molded parts set by the
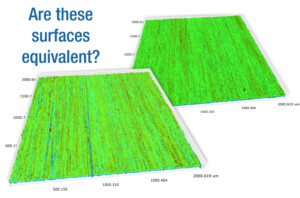
When switching from metal to plastic, does the texture stay the same?
July 30, 2024Download this article as a PDF Companies regularly need to replace metal components with plastics for reasons of weight, cost, performance, corrosion, etc. Very often, however, when the material is
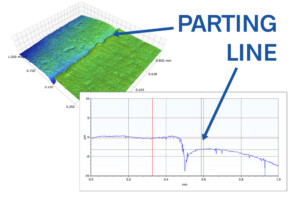
Controlling parting lines in molded plastics
July 22, 2024In plastic molding, parting lines can form on the component where portions of the mold meet imperfectly. These ridges and/or valleys may lead to several types of functional problems with
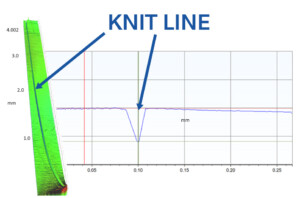
Controlling Knit Lines in Plastic Molding
July 15, 2024In the molding process, knit lines form where the material does not weld together seamlessly as it moves through the tooling. The cause may be related to the mold surface,
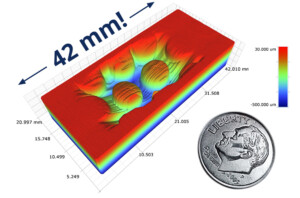
High-Res, Large FOV…and High Speed, too?
June 17, 20243D optical profilers provide high-resolution measurement of surface roughness and shape. Earlier optical profilers were limited by the size of their measurement areas (Field-of-view, or FOV), typically less than 1mm