Abrasive wear can greatly impact the performance of engines and machinery. This kind of wear can be caused by excessive roughness on either of the contacting surfaces. However, just looking at roughness may not give you the complete story.
When we define roughness, we typically exclude longer spatial wavelength structures that may also advance wear. As an example, we stitched a measurement around the circumference of one of the lobes of this camshaft, using our NP Flex optical profiler (Bruker):
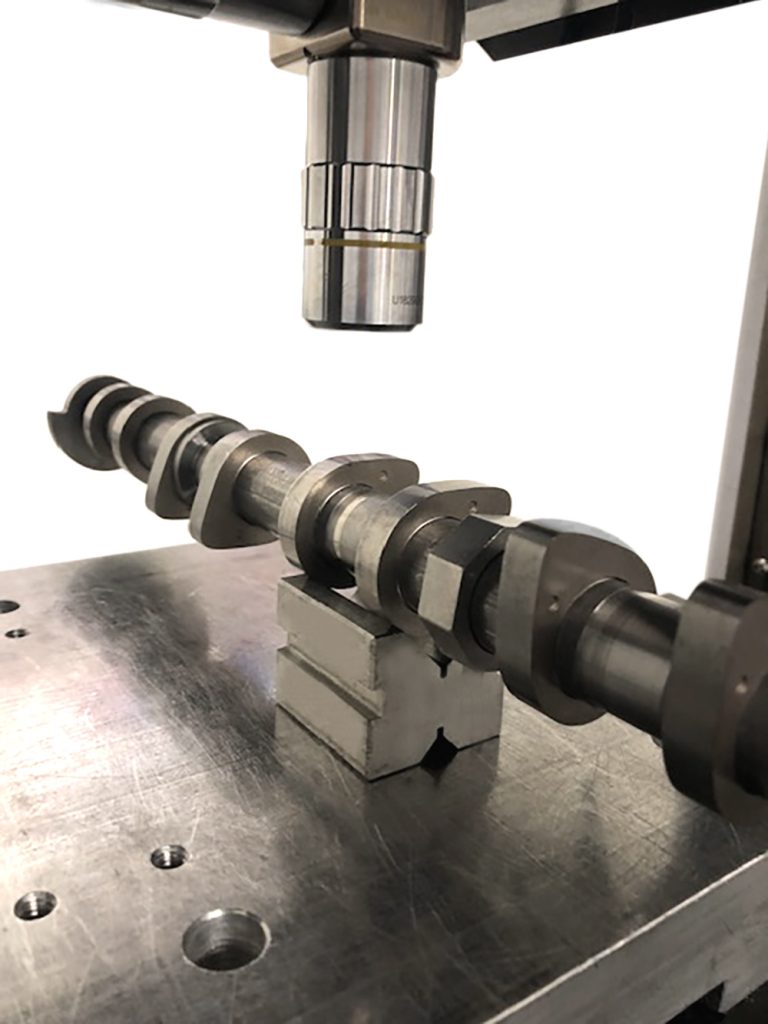
Here is the unfiltered measurement of the lobe surface:
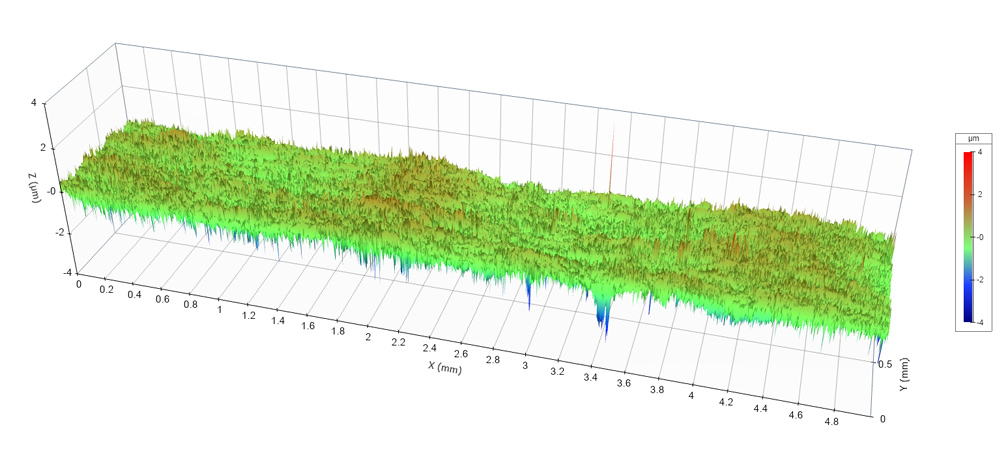
You can see in this measurement both the short spatial wavelength roughness and longer “waviness” undulations. If we want to look at the roughness, and roughness parameters such as Ra (average roughness), we might apply a 0.8mm long cutoff filter. And, in fact, that would give us a nice, consistent roughness surface:
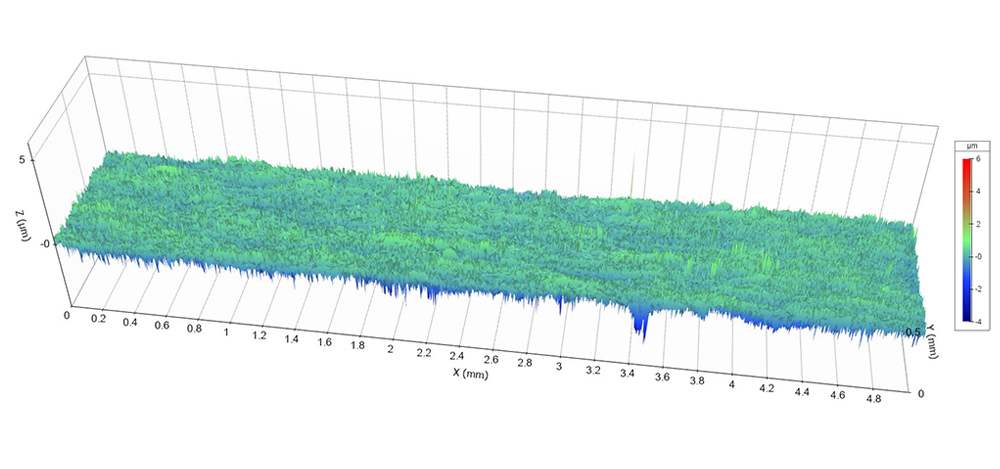
Everything looks good, right? But in getting to that seemingly smooth surface, we’ve filtered out the longer spatial wavelength features. Here’s what has been removed:
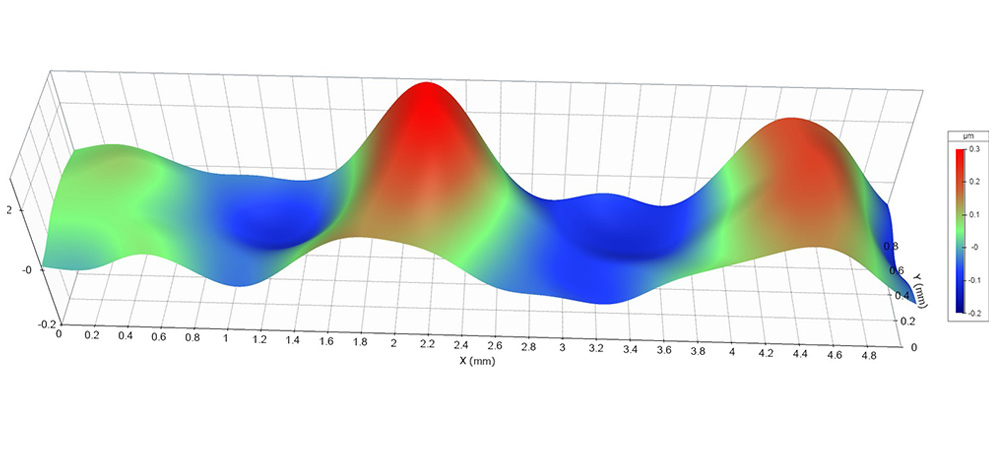
In rotational engine components, that waviness ( in this case, with approx. 2mm spacings) can lead to vibration and chatter that may greatly accelerate wear. If you’re only monitoring the roughness (the shorter spatial wavelengths), structures on this spatial wavelength scale will go completely unnoticed, and uncontrolled—and that can lead to a host of quality and warranty concerns.
You can learn more about roughness, waviness, and filtering on our website, and in our upcoming Surface Roughness, Texture, and Tribology class
You can read more about it in this recent article, “Waviness Affects Friction and Abrasive Wear” (Li, Garabedian, Schneider, Greiner).
Please fill out the form below to download this article as a PDF: