Applying the Material Ratio parameters — case study
In our post of a few weeks ago we discussed the Stylus (X,Y) parameters, which are derived from the 2D Bearing Ratio Curve. The Bearing Ratio curve shows the relationships between the peaks, core roughness, and valley regimes of a surface’s texture. The parameters Rpk, Rk and Rvk give the height of the peak region above the core roughness, the peak-to-valley height of the core roughness, and the depth of the valley region below the core roughness, respectively.
The three dimensional counterpart to this analysis is the Areal Material Curve, which is defined in the ISO 25178-2 standard. In this case, Spk is the height of the peak region above the core roughness, as measured over an area rather than along a single trace. Similarly, Sk represents the peak-to-valley height of the core roughness, and Svk is the depth of the valleys region below the core roughness, measured over that same area.
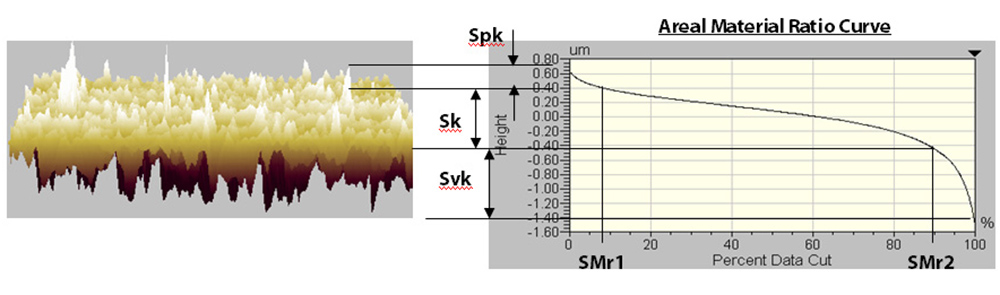
Using Spk, Sk, Svk to describe clutch plate texture
To understand how Spk, Sk and Svk can be applied it is helpful to look at an example application.
Clutch mechanisms are used to engage and disengage an engine with the drive train to transfer torque from the engine to the wheels. Clutches include steel “reaction” plates that engage against friction plates, which are usually comprised of paper or other fibrous material.
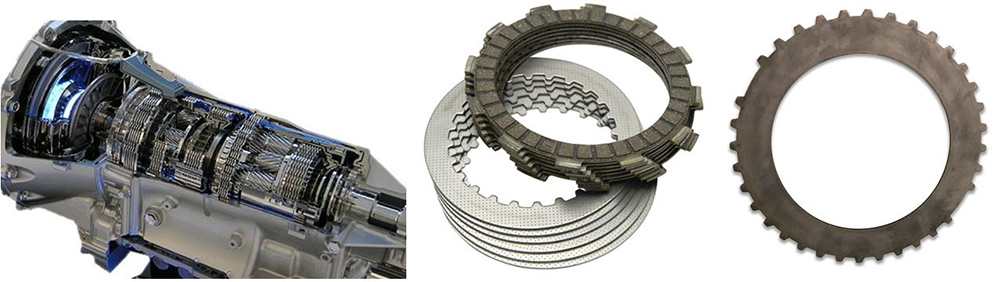
A transmission’s clutch mechanism includes steel reaction plates and fibrous friction plates.
The surface texture of the reaction plate is critical because it affects the engagement friction, the magnitude of the friction coefficient, interaction with the transmission fluid, engagement noise/shudder, and frictional material durability.
During manufacturing the reaction plate undergoes various processes to optimize the texture. Shot peening, for example, is commonly used to create an isotropic surface with no sharp peaks. Other processes such as laser texturing and abrasive belt finishing may also be employed.
One of the goals of this texturing is to optimize the fluid flow while the plates are separated, while also augmenting the fluid squeezing out from between the plates when they engage. To minimize shudder and fadeout, manufacturers also need to control the real area of contact while the plates engage. Longer wavelength waviness and shape near the plate edges will also affect fluid flow and engagement stability.
Measuring clutch plate texture
Clutch plate texture is typically measured using either a stylus profiler or a 3D optical profiler. The stylus can provide a long trace across the surface, showing long wavelength waviness. An optical profiler, however, can acquire data over an area to show directionality, isotropy, and finish consistency across the plate. Optical profiler measurements can also be stitched together to measure waviness.
The image below shows an optical 3D measurement of an area of the reaction plate surface. The texture is shown at increasing magnification, with the size of the field of view shown for each magnification.
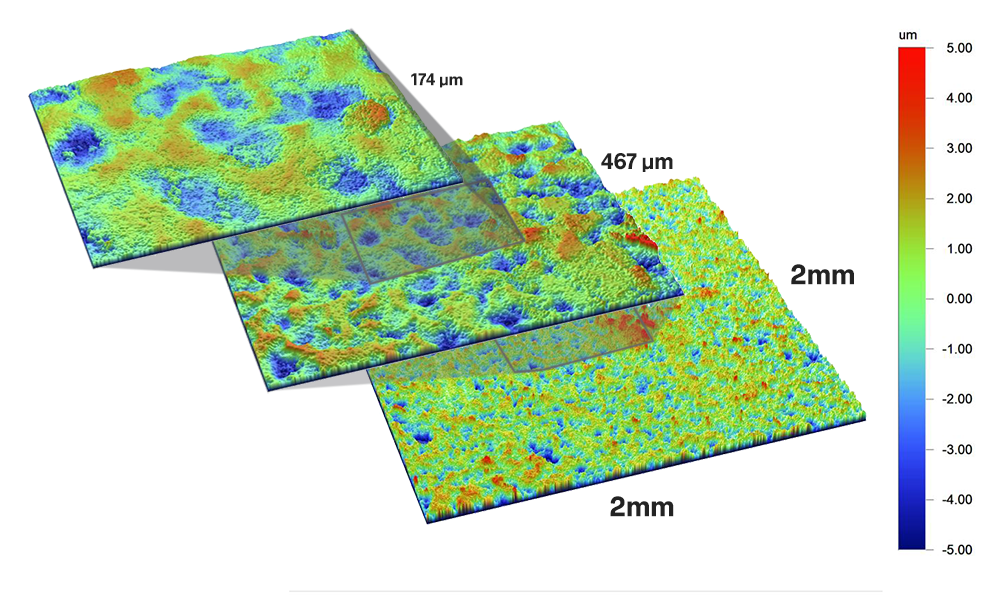
3D optical profiler measurements of a reaction plate’s shot peened surface. The three images show progressively higher magnifications.
Clutch designers and quality inspectors can use the Areal Material Curve to control the relationship between the peak, core roughness and valley regions. For example, Spk (which describes the peak heights above the core roughness) can be used as an indicator of the friction engagement between the plates. A high Spk value indicates that a surface has a preponderance of peaks, which may initially increase the friction between the surfaces. As the clutch plates wear, this peak material will be removed to an extent. Spk can therefore also be a good measure of the material that will be removed during wear-in.
Svk (the valley depths below the core roughness) can be used as an indicator of how well the surface will retain transmission fluid. It can also be related to the surface’s tendency to move debris away from the contacting surfaces.
The chart below shows the Areal Material Curve for the 2mm x 2mm area of the reaction plate shown above.
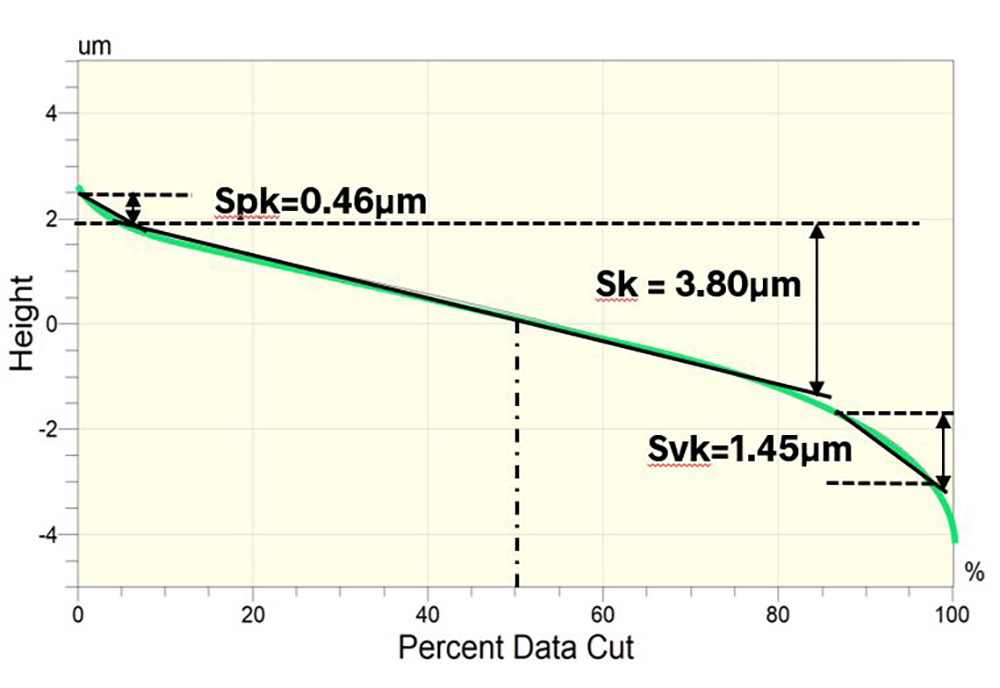
The areal material curve for the shot peened surface. Spk, the height of the peak region, gives information regarding friction engagement, while Svk, the depth of the valley region, indicates how the surface may retain transmission fluid.
Read more about Spk, Sk, Svk and the Areal Material Curve in the Texture Parameters Glossary.