In plastic molding, parting lines can form on the component where portions of the mold meet imperfectly. These ridges and/or valleys may lead to several types of functional problems with the molded part.
Appearance
The eye is very good at detecting small steps and lines. We can easily see even small parting lines, which may be perceived as a sign of poor quality to end users.
Sliding
A parting line ridge may inhibit the smooth movement of a sliding interface. As an example, a sliding component caused an audible click as it moved, as well as a tactile vibration. Using a 3D optical profiler, the quality team traced the issue to a small step in one of the sliding components, as shown in the image below. Though the step was only 12 µm high, the perception of poor quality it caused was a serious concern for the manufacturer.
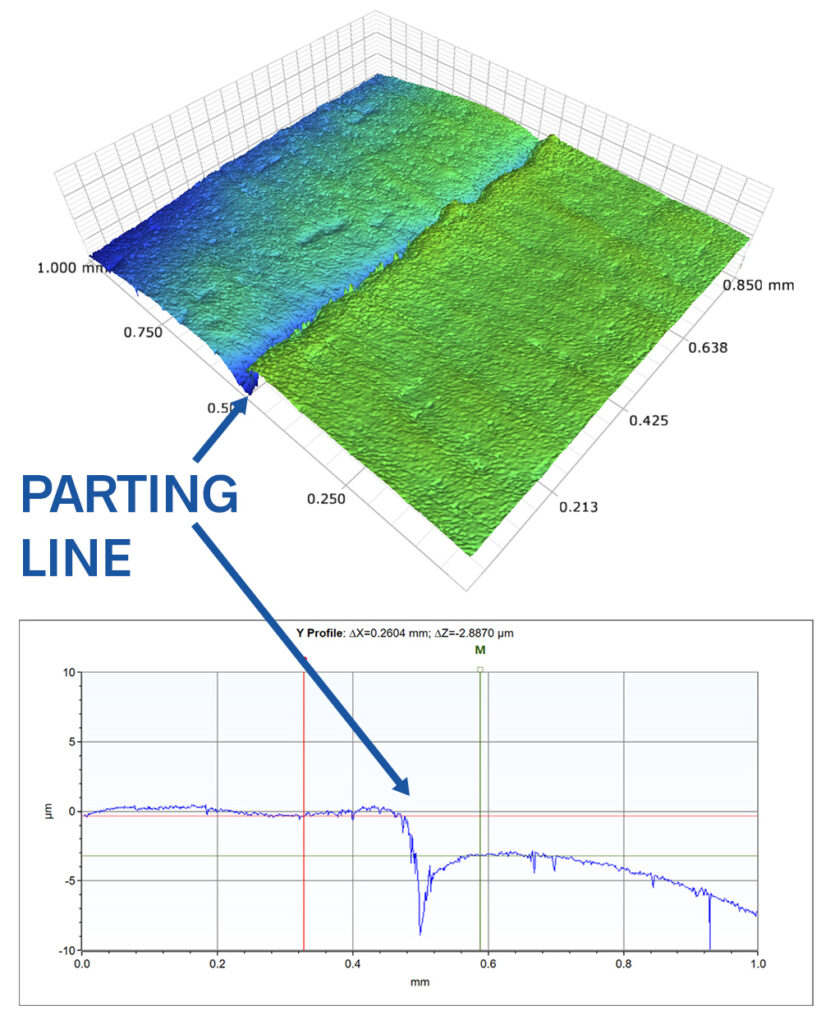
This small parting line caused an audible click— a quality issue for a sliding component.
Fit
A parting line, or a step created by misaligned mold components, can also lead to fit issues. The excess material can prevent a component from properly seating or registering with a mating part.
Sealing
A parting line or step can create a leak path that may not be detected by roughness measurements. The image below shows a valley created by a parting line. If this imperfection occurred in a hose connection, for example, the hose may not be able to conform to the flange or connector in the area of this valley, leading to a leaky interface.
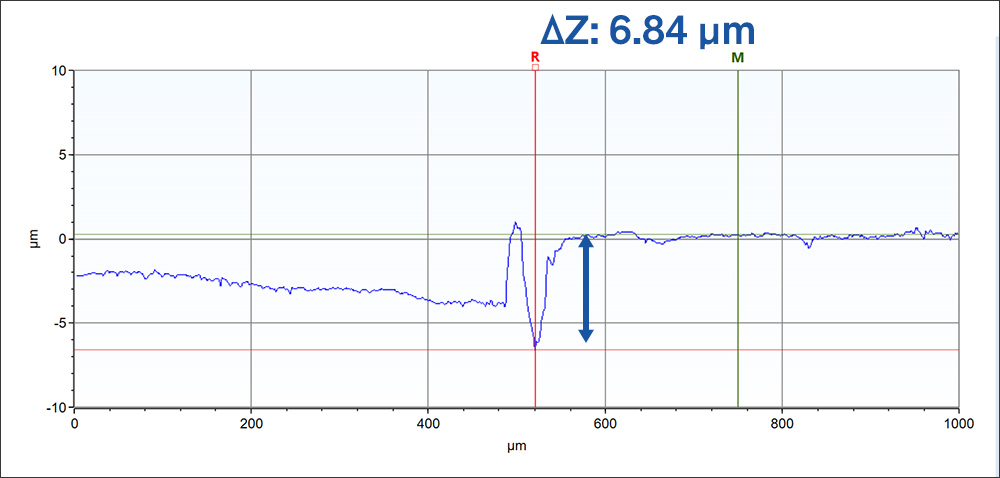
The valley created by this parting line could represent a leak path.
Challenge of measuring parting lines
In many cases, the surface finish specification for a molded part may only include a single surface roughness parameter such as average roughness (Ra, or Sa). But small parting lines can easily go undetected by Ra measurements because the small defects may fall entirely outside of the measurement area. This can be particularly true with 2D stylus measurements which only acquire a single measurement trace across the surface (and therefore can easily be completed without crossing a parting line at all).
Large area, 3D surface measurements (like the 3D measurement above) are more likely to capture parting lines. A stitched measurement with a 3D optical profiler provides sufficient lateral resolution, vertical resolution, and measurement area to locate and quantify small parting lines and ensure that they can be corrected.
As with knit lines and other defects, measuring the mold directly can help uncover the source of the error. Some 3D optical profilers, such as Bruker’s NPFlex, include a tiltable measurement head and long working distance objectives that allow inspectors to access challenging areas of complex molds. These direct measurements help prevent parting lines and other imperfections before they occur, rather than correcting them after components have been molded.
Want to know more about controlling surfaces for sealing, fit, appearance, and other functions? Check out our Surface Roughness, Texture, and Tribology Classes! The next class is coming up, so register soon to save your seat!