Scientists and philosophers through the ages have struggled with the concepts of friction. Leonardo da Vinci studied many aspects of friction, bearings, etc. In one set of experiments, he tied a cord to a rectangular block and dragged it along a surface. He found, surprisingly, that dragging the block on its short side, or long side, or even on its largest face, made no difference in the friction whatsoever.
This was counterintuitive at Da Vinci’s time…and it can still be confusing today.
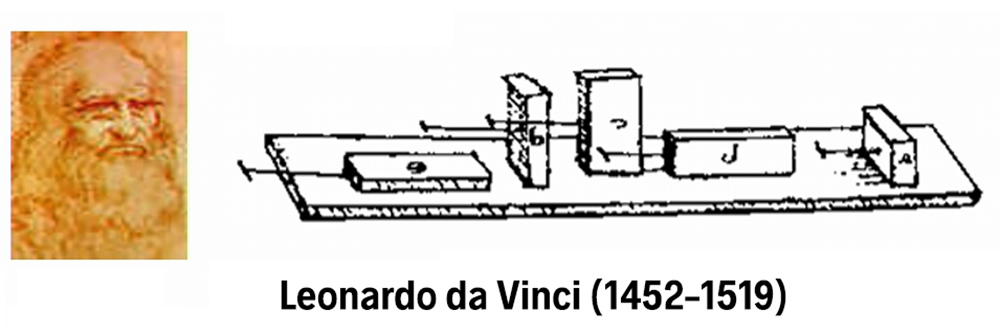
Fortunately, several centuries later, we have a better understanding of what is happening!
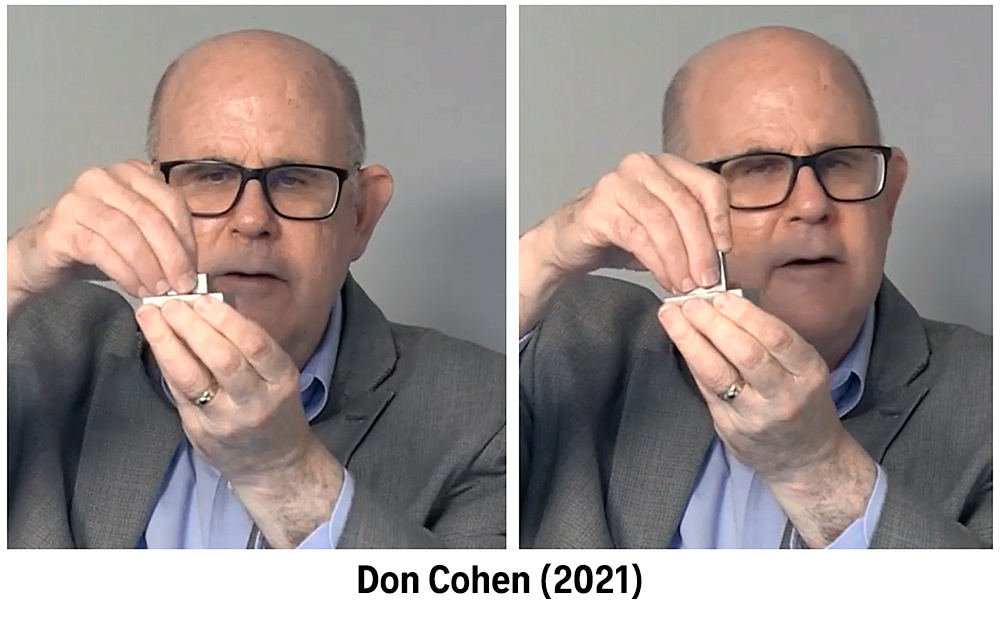
David Tabor and Frank Bowden spent a great deal of time researching the subject in the 1950s and 1960s. They came up with this thought experiment:
Imagine a surface with one sharp peak (or asperity). If a block is placed upon it, that one small asperity will resist the load. If the asperity can’t support the load, it will crush (i.e., it will plastically deform). The top block will drop down a little further, crushing the next asperities, and the next. At some point, the sum of the crushed areas will be sufficient to support the load. The cross-section of those crushed areas is what we call the real area of contact.
It turns out that the real area of contact under plastic deformation is typically very small relative to the apparent area of contact. For steel, the real area of contact is only about 0.05% of the apparent surface for a load of 200 pounds per square inch! The ratio differs for other materials, depending on their yield strength and hardness. Nevertheless, even for a softer material such as aluminum, the ratio is still less than 2% (for 200 PSI). Bowden summed it up this way: “Putting two solids together is rather like turning Switzerland upside down and standing it on Austria. Their area of intimate contact will be small.”
Boden and Tabor’s research was also key to our understanding that friction is directly proportional to the adhesion and interactions that are acting at the real area of contact under shear.
This gives us an important insight into why da Vinci saw no difference in the friction if his blocks were standing up or lying on their faces. Whether that apparent area of contact was large or small, the real area of contact remained the same, small area. That area may be distributed differently if the block is standing up or on its face, but nevertheless, the total real area of contact would be the same.
At 1:1…it’s more like Iowa
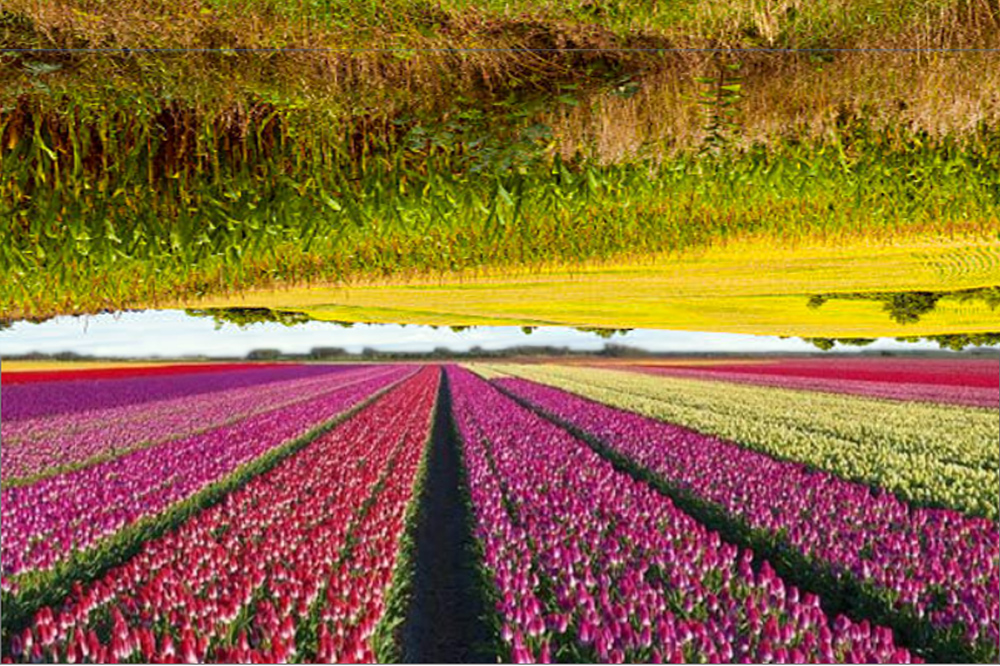
As a real-world example, here is a clutch plate and and rotor at a typical scaling…
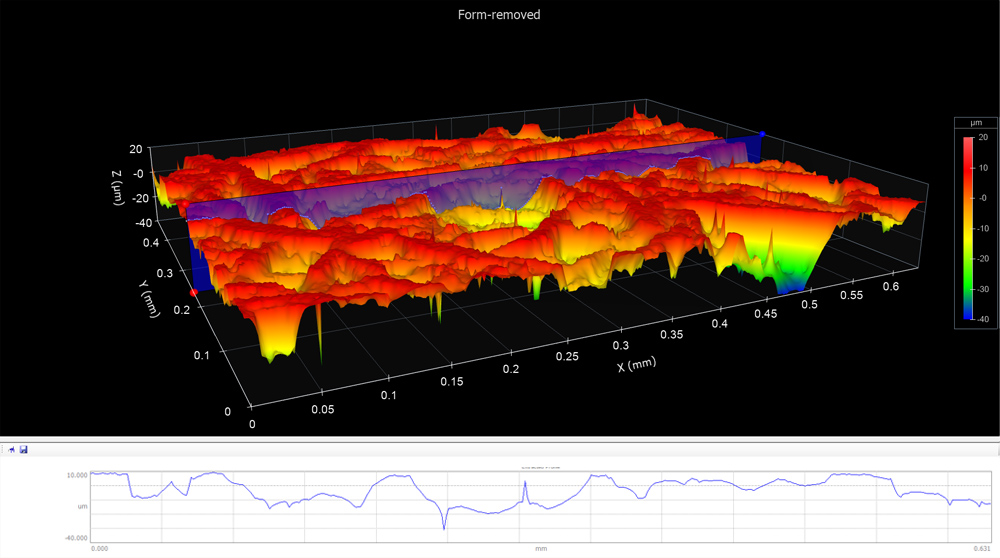
…and again at 1:1 scaling:
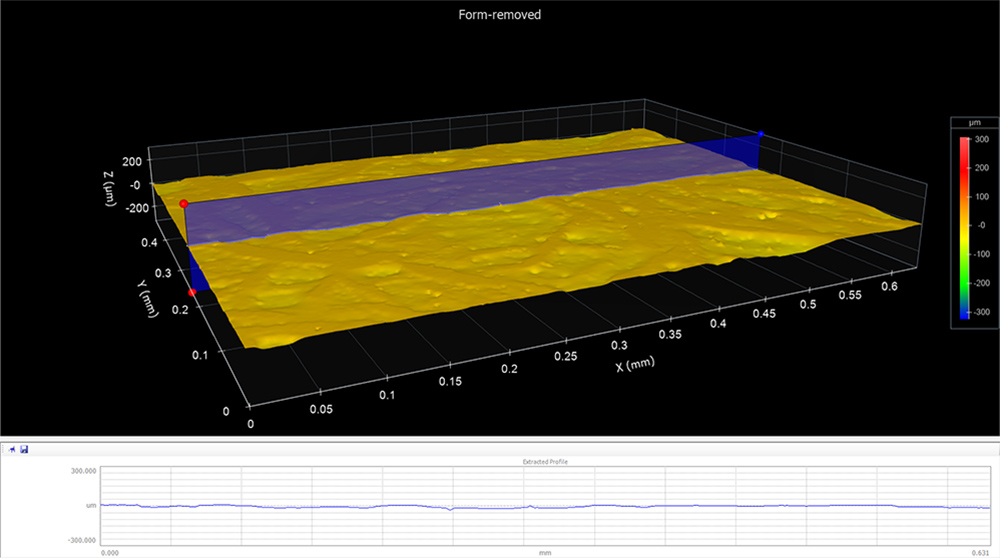
These images are courtesy of OmniSurf3D software (Digital Metrology Solutions).
We go into this topic in depth in the Dry Friction module of our Surface Texture and Friction classes. The module, and all of the class modules, are available on udemy.com.
1. Thomas, T. (1998). Rough Surfaces, 2nd Edition (2nd ed.). World Scientific Publishing Company. Retrieved from https://www.perlego.com/book/850529/rough-surfaces-2nd-edition-pdf (Original work published 1998)