It’s a common intuition that smoother surface texture is “better” for rotating or sliding over another component. It seems natural that a smoother surface would wear less, have lower friction, and perhaps operate at lower temperatures.
This gut reaction is widespread and runs deep. As an example, a few years ago a medical device was developed with a “rougher” surface that improved fluid retention and thus provided better wear characteristics. Yet, the device was widely rejected by surgeons because the rough surface looked “bad” while the typical smooth surfaces looked “good.”
Whether smooth is better is, of course, a complicated question, and the answer will depend on the material properties as well as the surface texture. If the texture of one or both surfaces in a sliding interface is very smooth, there will be a large area of contact between the surfaces at the microscopic level. This large area of real contact will make the surfaces likely to stick, and therefore likely to wear.
At the other extreme, a surface consisting of tall, narrow peaks may act as a “micro-saw” that can abrade the mating surface as it slides over it, particularly if the “saw” surface is made off the harder material.
For a given application there will be some optimal texture in order to carry a load safely without sticking or digging in.
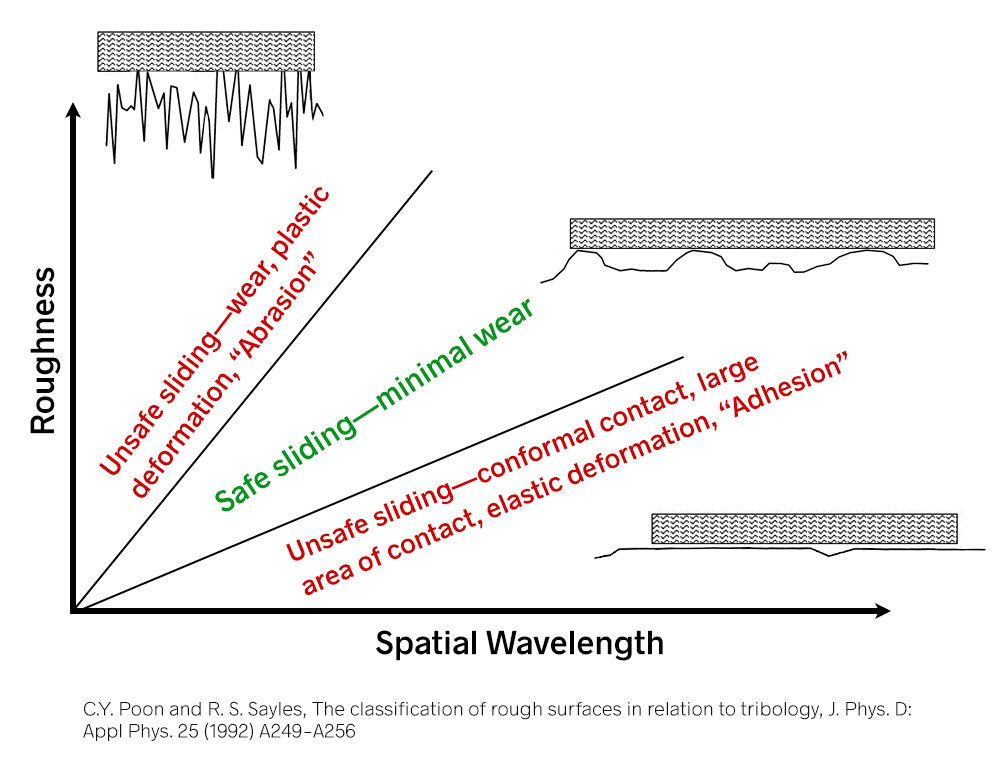
When designing that optimal surface, engineers must also consider how the surfaces will change over time. During the run-in period, newly manufactured mating surfaces undergo substantial change as they see service for the first time. Peak material is worn away as the surfaces conform to each other, and the surface roughness will change, becoming either smoother or rougher. Engineers need to design a surface for performance both before and after the run-in period. If a surface gets rougher as it wears in, it may need to be smoother initially, and vice versa.
There are many other considerations as well, including, system loads, the size of the debris particles generated as the surfaces wear, lubrication and texture to retain it, etc. We look at these and related topics in the Wear, Dry Friction and Lubricated Friction modules of our Surface Texture and Tribology short course. The full course, and the individual modules, are available on udemy.com. I encourage you to have a look.