The Average roughness parameter (Ra, or Sa for areal 3D measurement) cannot always distinguish between surfaces with deep valleys, high peaks, or variable heights across the surface. So how do we reliably differentiate these surfaces to know whether we are making good parts or not?
Sometimes the best way to control a process is with a combination of more than one parameter.
In the early 1990s researchers Tim Hegemeir and Mike Stewart were studying how cylinder liner texture relates to diesel engine characteristics.1 They began by examining the parameters derived from the bearing ratio curve (Rpk, Rk, and Rvk) to understand how they related to performance issues. They found that the symmetry of the bearing ratio curve (that is, the relationship between the peaks, valleys, and core material), related to oil consumption and cylinder liner wear, sometimes more than the amplitudes of the peaks and valleys. That symmetry could be described using a ratio of parameters, such as Rvk/Rk.
For areal (3D) measurements, the material ratio (bearing ratio) parameters Spk, Svk, and Sk, describe the peak, valley, and core material of a surface. The ratios between these parameters give a good indication of the symmetry of the bearing ratio curve. For example, Spk/Sk (the ratio of the Reduced Peak Height to Core Roughness) shows the relationship between the peak material and core material. In the example below, two surfaces with identical Sa values can be readily distinguished by Spk/Sk.
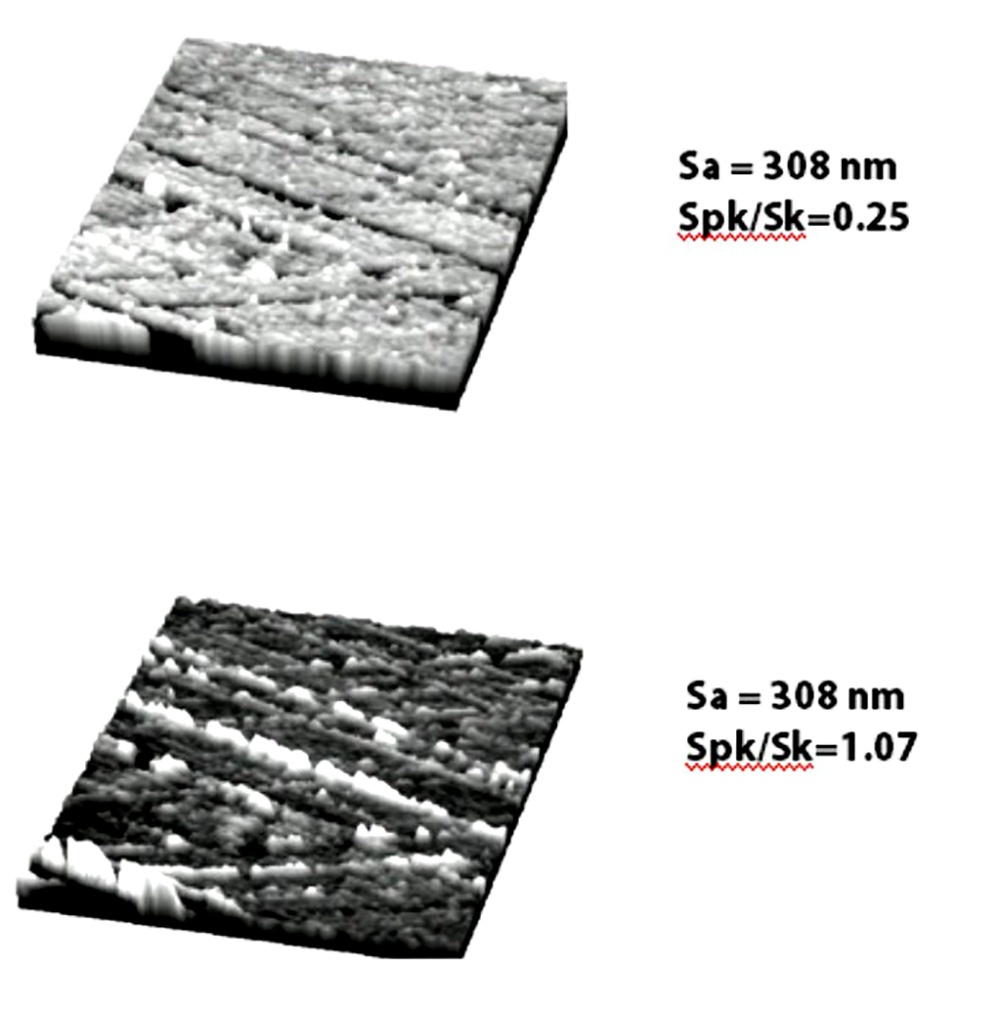
As an example of its application, in a seal, a surface with a large Spk/Sk value may rip into the seal and cause leakage or failure.
Svk/Sk (Reduced Valley Depth to Core Roughness) can provide information about how well the surface will maintain lubricant and/or trap debris. Svk by itself tells us about the magnitude of the valleys, but it doesn’t give information about the overall surface amplitude distribution. Svk/Sk can provide a reality check by letting us know whether the surface amplitude symmetry is consistent with what we know to be a good part.
The third ratio is Spk/Svk (Reduced Peak Height to Reduced Valley Depth Ratio) which gives the ratio between the reduced peak height and reduced valley depth.
I began working with these ratios in the 1990s, first in spreadsheets, and then later in software packages such as Bruker Vision 64 (then Wyko Vision32) and Digital Metrology’s OmniSurf3D. The ratios prove useful in applications such as seals and bearings because they differentiate surfaces with similar Sa but different texture amplitude symmetry.
Take the case of “structured” surfaces, such as those found in hydraulic piston bores. These surfaces strike a careful balance between peak, core, and valley material, to simultaneously minimize sliding friction, maintain lubrication in the interface, and provide sealing. In some applications, the performance is more sensitive to symmetry than to magnitude. Surfaces with very different average roughness values may perform similarly if the symmetry is the same.
The example below shows a surface with a “plateaued” upper region cross-hatched by valleys. The upper region of this surface, however, is actually more akin to a series of mushroom caps than to a flat plateau. The ratio of Spk/Sk may help distinguish this surface from one with a flatter plateau, which could prove critical for the surface’s sealing or wear characteristics.
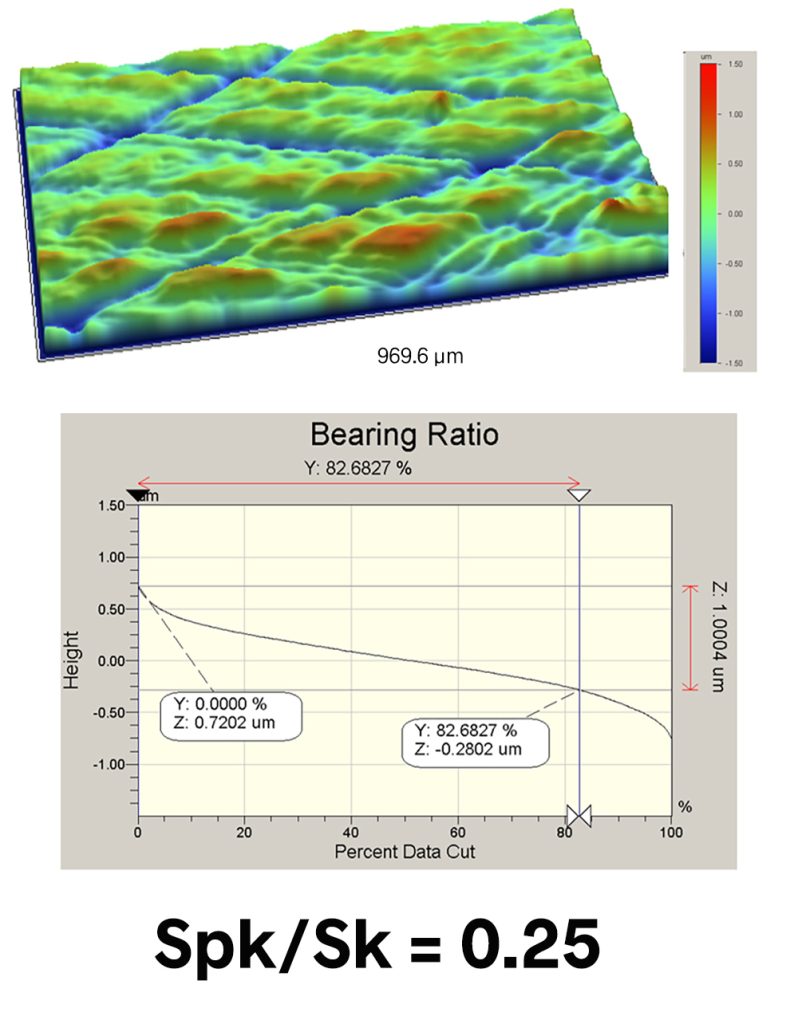
While these ratio parameters are not part of standards, their components Spk, Sk, and Svk certainly are. Using the ratios requires that everyone involved in the process understands what the parameters mean, how they are interpreted, and how they are intended to be used.
To learn more, visit the Surface Texture Parameter Glossary on this site. The specific pages to reference are Spk/Sk, Spk/Svk, and Svk/Sk.
- Tim Hegemier and Mike Stewart, Some Effects of Liner Finish on Diesel Engine Operating Characteristics, SAE 93076 , March 1993.