When we think of how to measure wear, the first thought might be to quantify how much material has been removed from a surface. We might look at a change in average roughness, say, to get a sense of how much peak material has been removed through contact with another surface. Or, we may use parameters derived from the bearing ratio curve to estimate the volume of material in a wear scar.
But “wear” is not always a process of material removal. Material may also be redistributed, or even added, depending on the wear mechanism. In the broader sense, wear is a progressive modification to a surface, be it a loss, deposit, or redistribution of material.
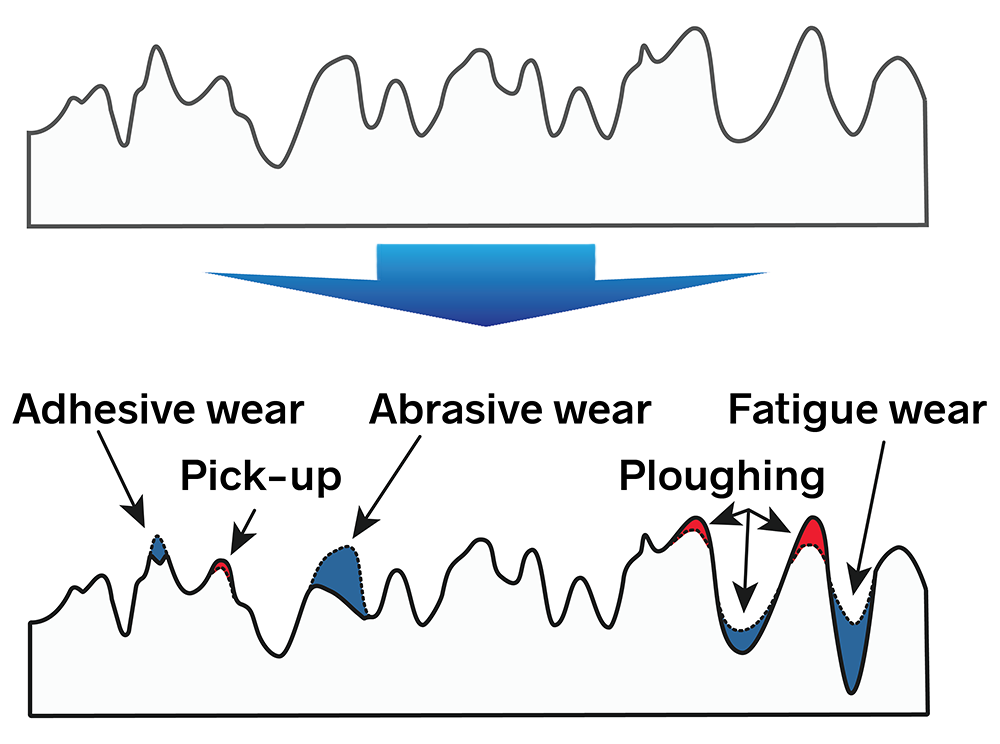
Moreover, these mechanisms may all be occurring simultaneously: abrasion may remove material while adhesion is depositing it. Fatigue wear may result in “cracking,” forming valleys without affecting the surrounding peak structures. “Plowing” may result in peak material being created as valley structure are being formed. A parameter such as average roughness (Ra, Sa) may decrease as peak material is worn away by abrasion, but it may increase as well due to adhesion!
In short, wear cannot be treated as a single number that increases or decreases. It is instead the result of many mechanisms acting on a surface. Understanding the impact of wear on a part’s performance may require a number of different parameters, possibly different parameters depending on the particular stage of the component’s life cycle.
Want to know more about wear? Check out the Wear Mechanisms, Measurement and Specification module of our full Surface Texture and Tribology short course on udemy.com. We discuss wear mechanisms and methods to quantify, predict and control wear over time.