One of the great challenges of product design is accurately assessing how a component will wear in order to maximize its useful lifetime.
Wear is, of course, caused by a wide variety of mechanical, chemical and environmental factors. Daily, ongoing wear may be punctuated by periods of brief, intense stress, unexpected exposure to environmental agents, or user abuse. Nonetheless, engineers must account for as many of these effects as possible and attempt to mitigate them to extend product life. Achieving that goal requires good data on how, and why, a component wears.
Organic wear vs accelerated wear
The most accurate way to assess component wear is to retrieve and analyze a sampling of product from the field. These parts will have experienced the hazards of use in the actual application, including environmental changes, a variety of user interactions, etc. However, it is not always possible to obtain a representative sample of organically worn parts within a reasonable time frame.
Another common option is to accelerate wear through mechanical methods. Such “tribological testing” provides feedback on wear much more quickly than acquiring data from actual use, and it can show the procession of wear over time as well. Though some aspects of wear can be simulated, this kind of testing may not account for changes to the material over time, environmental cycles and user interactions that directly affect durability.
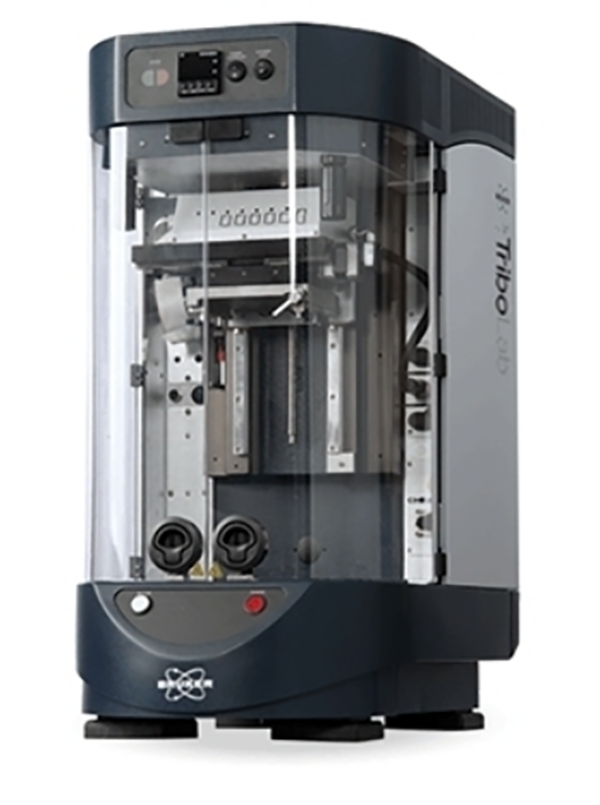
A tribological testing station makes it possible to accelerate wear in a controlled fashion (Courtesy Bruker, Inc.)
Wear measurement example: sensors
Many types of sensors rely on a mechanical contact, such as a “button” or “fingers” sliding against a resistive element (e.g., “conduction ink”). These sensors need to be able to provide consistent, accurate readings over their lifetimes, despite wear from constant abrasion, chemical interactions, etc.
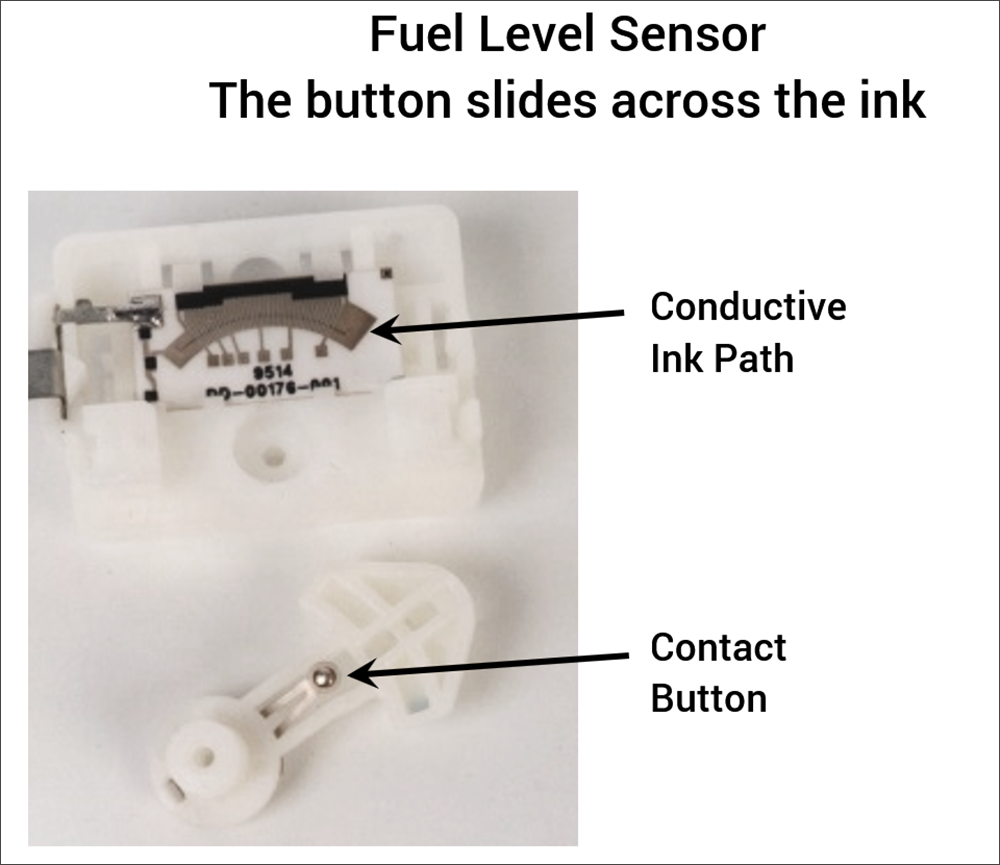
The components of a fuel sensor. The contact button slides over the conductive ink.
Manufacturers must consider each component to ensure long sensor life. The geometry of the sliding contact, as well as its texture and material, must be carefully controlled. The height, width and hardness of the conductive ink are all critical, as is the assembly load between the contact and the conductive ink (the “preload spring”).
The image below shows measurements of the components of a sensor of the type shown above. The measurements were made using a 3D optical profiler, which provides both excellent resolution and sufficient vertical range to measure these components.
The contact button shows only marginal scuffing, well within acceptable limits for the given wear period. No significant change to the contact’s radius of curvature was detected, indicating that the contact has not undergone excessive vertical force.
The wear scars in the conductive ink (caused by the motion of the contact button) appear deep and potentially concerning. However, upon analysis the depths of these trenches were also found to be within acceptable limits.

The wear to this sensor’s contact and ink are clear in these 3D optical profiler measurements. However, upon analysis, the wear on both components was found to be within acceptable limits.
The examples below show other sensors of a similar type which did, in fact, fail in the field. The excessive wear in the conductive ink is clear in both cases. A change to materials, hardness, or the spring load of the contact button would be possible considerations for rectifying the problem in future generations of the sensor.
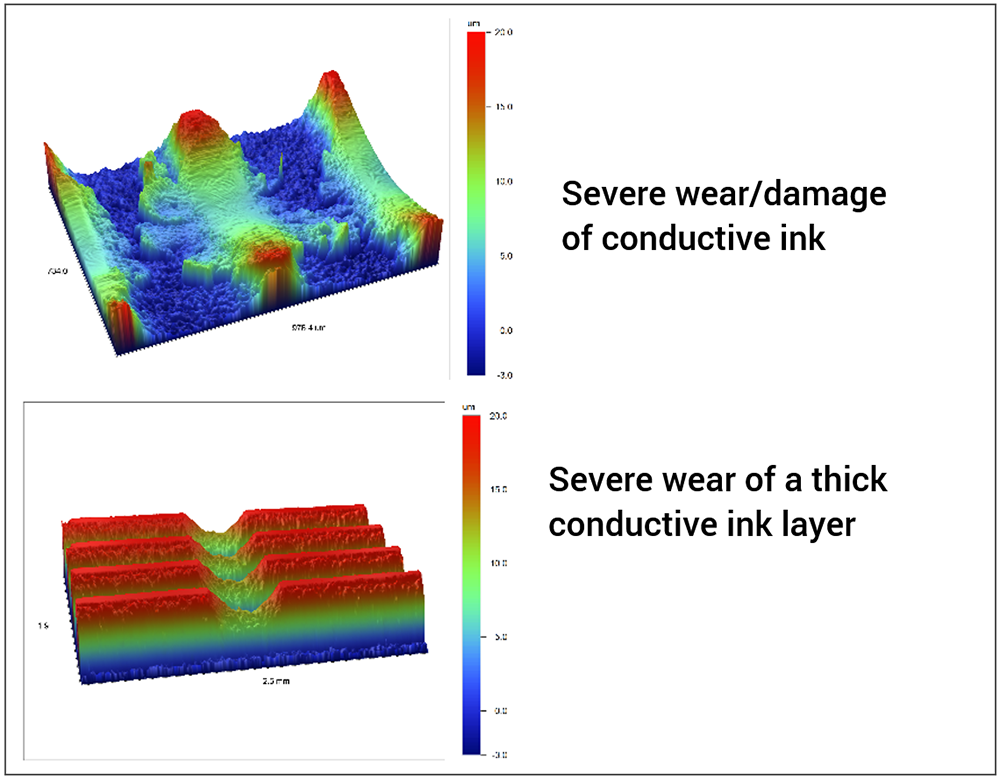
Excessive wear in the conductive ink lead to premature failure in both of these sensors.
Drawing the right conclusions from wear data
As we’ve seen, accurate wear measurement requires a representative sample of parts, a reliable method for generating wear, and repeatable measurement equipment and techniques. Drawing the correct conclusions from wear measurements, however, is an even more daunting task, one that requires years of experience with the specific parts and with wear in general.
At Michigan Metrology we have measured wear on thousands of parts over the years, both to address production-line issues and to diagnose premature wear in warranty cases. We invite you to contact us about how we can help with your wear concerns.
You may also want to check out our Surface Texture and Wear Classes which are held live 1-2 times per year, and are available online as well, for a wealth of information on the topic.