Companies regularly need to replace metal components with plastics for reasons of weight, cost, performance, corrosion, etc. Very often, however, when the material is switched, the surface roughness specification stays the same. This practice can result in a number of quality and functional issues.
Take the case of a fitting for a pressurized hose. Say the manufacturer needs to switch to a plastic material for lower cost and material compatibility. The new plastic part has the same surface finish as the metal fitting. Yet, in the field, the plastic parts leak. How can this be?
Manufacturing methods affect finish
Most often the issue begins with the surface finish specification. These specs are frequently based on a single roughness parameter such as Ra (average roughness). This is particularly true for mature products that may have been developed decades ago.
Here are two surfaces with similar average roughness values, and both have a similar “striped” appearance. Yet, the spacing of stripes on the upper right surface is twice as wide as the pattern on the lower left surface. This difference may affect fluid flow and wear characteristics—yet an average roughness measurement would not spot the change.
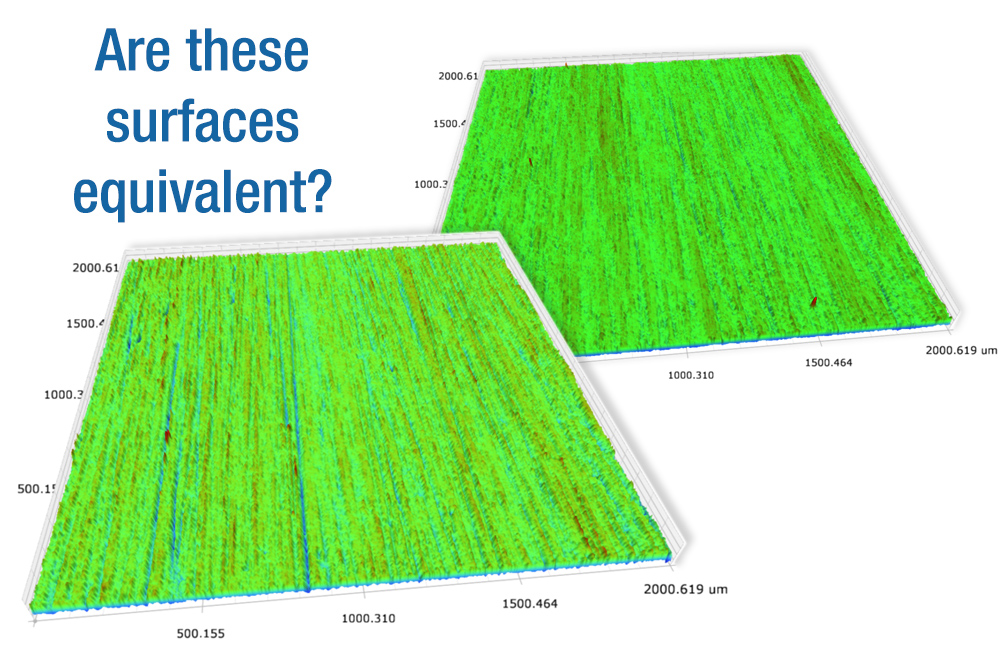
The differences in finish caused by machining processes or the movement of plastic through a mold impact functionality. A change in measured parameters, and possibly different measurements, may be required to continue to control performance.
Waviness
Other aspects of texture may also be important for function. Longer spatial wavelength shape (i.e., waviness) can also be introduced by new tooling. A roughness measurement will likely miss differences in these longer spatial wavelengths which, undetected, can lead to sealing issues, chatter, etc.
Materials
Different materials can also affect function in the interface. Differences in the surface energies between the metal and plastic surfaces may affect how the flowing fluid will wet the surfaces—despite the surfaces having similar dimensions and texture. The surface texture will tend to magnify the degree of wetting.
Take the case of gasoline or brake fluid on a metal surface. These fluids have very low surface energy, so they will tend to wet the metal surface well. If we now switch the component from metal to plastic, the fluids will still wet the plastic, but potentially not as well. Adding texture to the plastic surface may, in this case, improve the wetting.
The interaction of material and texture
The final surface texture will be a product of the physics and chemistry of the molten plastic flowing through the mold/tool, thermal effects, and the subtle texture introduced by finishing processes.
The complex interactions between material and texture need to be considered when the component material is changed. Just as strength and dimensional specifications need to be reconsidered, the surface specifications need to be fully considered as well. Taking the shortcut of recycling the surface texture spec for a component formed in a new material may be a recipe for performance issues.
Want to know more about the relationships between surface texture and materials? Check out our Surface Roughness, Texture, and Tribology classes, which are available in person and online.