In this 3-part series we look at the case of dry, sliding friction and discuss how surface roughness and materials impact the surface as a bearing.
PART 2 Material Properties
In last week’s post we saw that surface texture impacts a bearing interface. Now let’s look at material properties.
As we’ve said, to make a good bearing we want to minimize friction while also minimizing wear. Two material properties will have a substantial impact on both:
- Young’s Modulus (Elastic Modulus, E) is a measure of the material stiffness
- Hardness (H) is a measure of the material’s ability to resist deformation.
Materials with high hardness and modulus, such as diamond, ruby, and steel, tend to produce a smaller real area of contact while also being durable. These are good candidates for bearings. Low-modulus materials such as rubber will produce large real areas of contact and therefore high friction, making for poor bearing surfaces.
Plastic vs elastic deformation
In a component such as a bearing, we want the material to deform elastically, rather than deforming plastically and wearing down. When the surface is undergoing elastic deformation, the real area of contact is affected by both the elastic modulus and the surface texture. On the other hand, when a surface undergoes purely plastic deformation, the real area of contact is only affected by the material hardness1 . We discuss the reasons behind this difference in the Dry Friction module of the Surface Roughness, Texture, and Tribology short course.
Plasticity
“Plasticity” indicates the tendency of the system to deform either plastically or elastically2. The Plasticity Index (Ψ) includes all of the material properties and texture characteristics we’ve discussed so far:
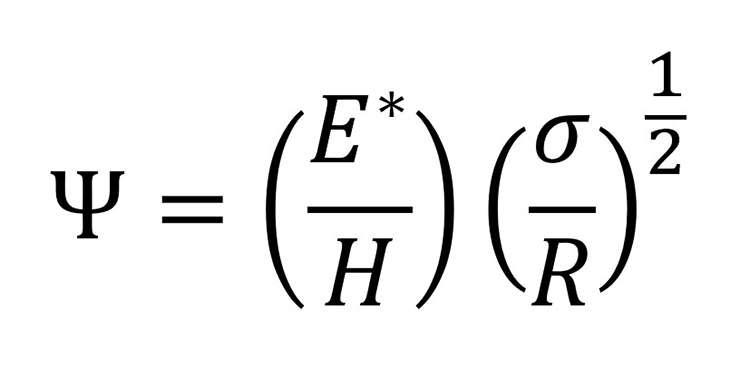
where
- E* is the composite Elastic Modulus of the materials in the interface
- H is the lowest hardness of the materials in the interface
- σ is the composite standard deviation of the peak heights (an indicator of surface roughness)
- R is the composite mean radius of curvature of the peaks within that surface (an indicator of the shape of the peaks).
This very useful equation combines the material properties (E and H) and surface texture properties (σ and R) that we know will impact the real area of contact, and therefore friction.
Next week, in Part 3 we will look at how we can use this equation to predict whether a material/surface texture combination will lead to a good bearing surface.
References:
- Frank Philip Bowden and David Tabor, Friction, An Introduction to Tribology, Robert E. Krieger Publishing Co. Malabar, Florida 1973.
- Greenwood, J. A. and Williamson, J.B.P (1966), “Contact of Nominally Flat Surfaces”, Proc.Roy.Soc Lond. A295, 300-319.
- Bharat Bhushan, Introduction to Tribology. John Wiley & Sons Ltd, New York, 2013.
- Ernest Rabinowicz, Friction and Wear of Materials, John Wiley & Sons, 1995.
Want to learn more about these topics? Check out the Surface Roughness, Texture, and Tribology short course.
Please fill out the form below to download this article as a PDF: