Fluid retention is a critical function of the surface texture in many applications. These surfaces may need to retain oil for lubrication, for example, or fluids may need to be precisely applied for printing or coating applications.
In these cases we need a method to quantify the “void volume” —the portion of the surface which can retain fluid. Areal (3D) measurement greatly aids our ability to quantify voids and porosity. An areal measurement will include the entirety of most pores and voids, so we can accurate, and repeatably, assess depth and lateral dimensions. A single trace from a stylus measurement system is unlikely to cross the widest or deepest part of a void, and repeating a measurement across the same point is difficult.
With areal measurement data we can use 3D functional parameters that predict surface capabilities, rather than simply calculating an aspect of the wave form such as average height or spacings. The Void Volume parameters are 3D functional parameters that were developed specifically to quantify the fluid-retention capability of a surface.
Material Ratio
The void volume parameters are derived from the material ratio curve (aka the Bearing Area Curve or Abbot-Firestone Curve), discussed elsewhere in the blog. The parameter mr is the material ratio, a measure of the amount of material a given depth into the surface. In the example below a plane has been pushed down 5µm below the highest peak. If the surface were worn down to this level, mr would be the area of the remaining plateaus divided by the total measurement area:
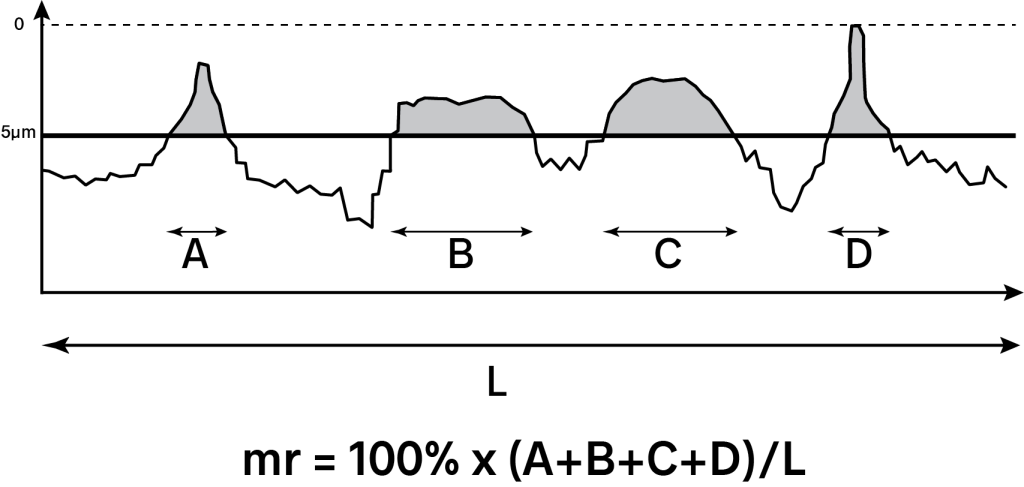
Void Volume Parameters
The Void Volume parameters are derived from the material ratio:
Vv(mr), the Void Volume, is the volume of space contained within the surface texture, starting at the depth that results in a specified material ratio, mr. For example, Vv(25%) is the volume of the voids below the level where mr = 25%.
Vvv(p), the Dale Void Volume, is the void volume below a depth at which p, the material ratio, is (typically) 80%.
Vvc(p,q), The Core Void Volume, is the void volume between two depths, p and q. P and q can be any values, thought typical values are p = 20% and q = 80.
The units for all three parameters are um3/um2, which is the void volume normalized by the cross section of the measurement area. Note that the units µm3/µm2 reduce to µm.
All three parameters indicate how much fluid would be required to fill the surface to a depth corresponding to a particular material ratio, and normalized to the measurement area.
In the illustration below, a solid (the gray area) has been placed in a square tub. The tub has been filled with water to a depth at which the material ratio is 25%, as shown. The void volume at this level Vv(25%) = 0.5 µm3/µm2. Another way to put this: if the solid were removed, VV is the depth of liquid which would cover the bottom of the tub (i.e., the measurement area).

Because the void volume parameters are normalized to the measurement area, their values remain the same regardless of the size of the measurement area, as long as the surface texture is essentially the same across the surface.
Application of the Void Volume Parameters
The void volume parameters are useful when considering fluid flow, coating applications and debris entrapment. A new surface may be specified by Vv(0%) which would indicate the total void volume provided by the initial texture. The Dale Void Volume may indicate the potential remaining volume after surface wear has worn down the peak material. The Core Void Volume may be useful to establish how much volume is available once a surface has been run in (i.e., after peaks have been worn down and valleys filled in with debris).
Learn more about these parameters, and other parameters derived from the Material Ratio Curve, in the Surface Texture Parameter glossary.