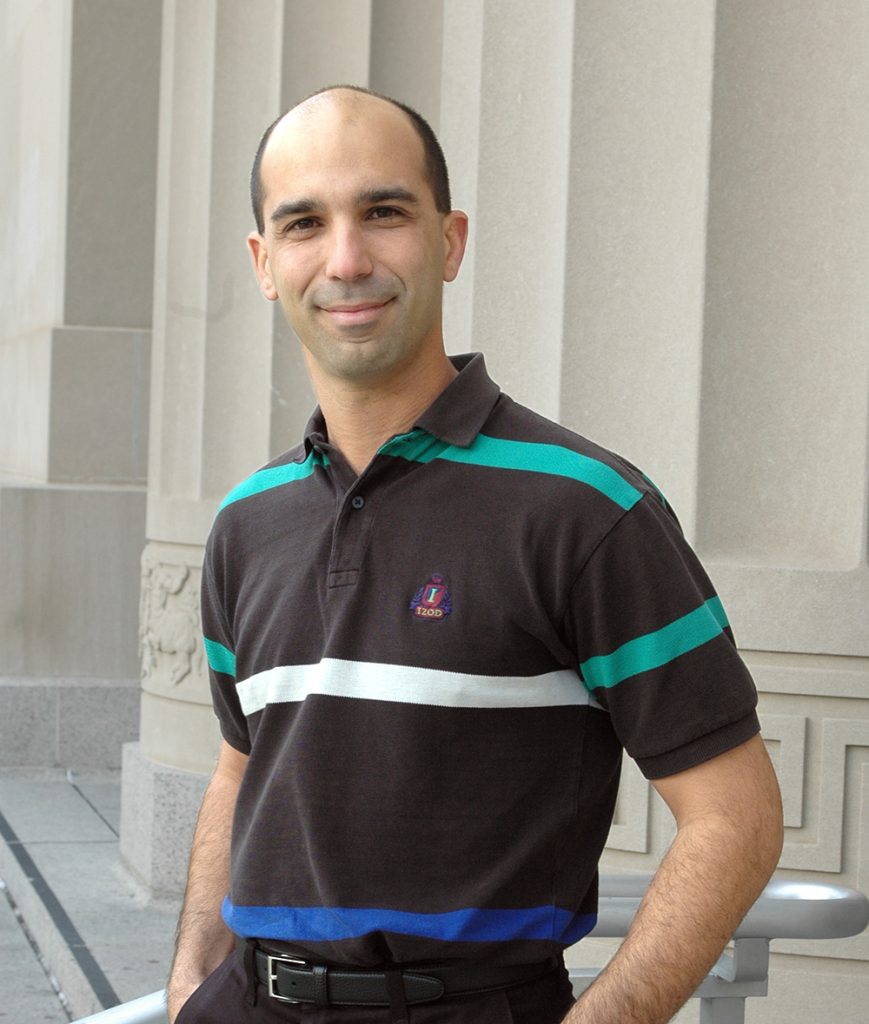
Where can your career take you after your first job has you designing Aston Martin engines? The answer is: everywhere!
Anthony Musci describes himself as a “serial entrepreneur,” having applied his engineering expertise and penchant for novel solutions to fields from racing to alternative energy. “If you had told me when I was in school that this is what I’d do in my career, I’d never believe it,” he says. Yet a combination of hard work, and a knack for being in the right place at the right time, has led Musci to an amazing career that is still in full swing.
Ford and Aston Martin Lagonda (AML)
After graduating in the early 90s in mechanical and aerospace engineering, Musci interned, and later took a full-time position, with Ford’s Advanced Powertrain unit. Through Ford’s College Graduate program, Musci gained broad exposure to many aspects of the business.
On one particular day, Musci was able to check out a ‘mockup’ prototype for a proposed V12 engine—and he noticed some issues. With “young engineer” fearlessness, he sent a memo to the chief engineer, several levels above his boss, with his suggested improvements. The memo had the felicitous outcome of getting Musci in front of the chief engineer, and soon he found himself in the whirlwind of starting the development of a design that would lead to the AML V12.
“You can’t believe what it took to get the car made,” said Musci. “If you’ve seen the movie Ford v Ferrari, from the inside it was ten times as crazy.* I had to learn fast.” After quickly building a small team for the endeavor, Musci’s focus included the cylinder block, oil system, cooling system, pistons, rods, crankshaft, and electronic controls. While each team member had specific responsibilities, “Each of us were fully familiar with all of the details of the entire engine and considered it our responsibility to be so in order to create a world-class engine.”
The team’s development effort was bolstered by new technologies just becoming available and practical at the time, including CAD/CAM, computer simulation, and rapid prototyping. Surface finish analysis, while basic relative to today’s standards, also helped drive the development of cams, shafts, seals, cylinders, etc. To examine bore surfaces at the time, the engineers needed to cut open engine blocks and view the finish under high magnification “with a lot of light.” Stylus measurement systems output 2D strip charts which showed the surface visually, providing more information than a simple average roughness number. The engine that came out of the program ultimately powered Aston Martin to win GT1 multiple times at the 24 Hours of Le Mans race, as well as powering cars in in several other categories to many other victories. But for Musci, “I realized that being part of helping so many people at AML have a bright future once again was by far my proudest achievement of the entire V12 program.”1
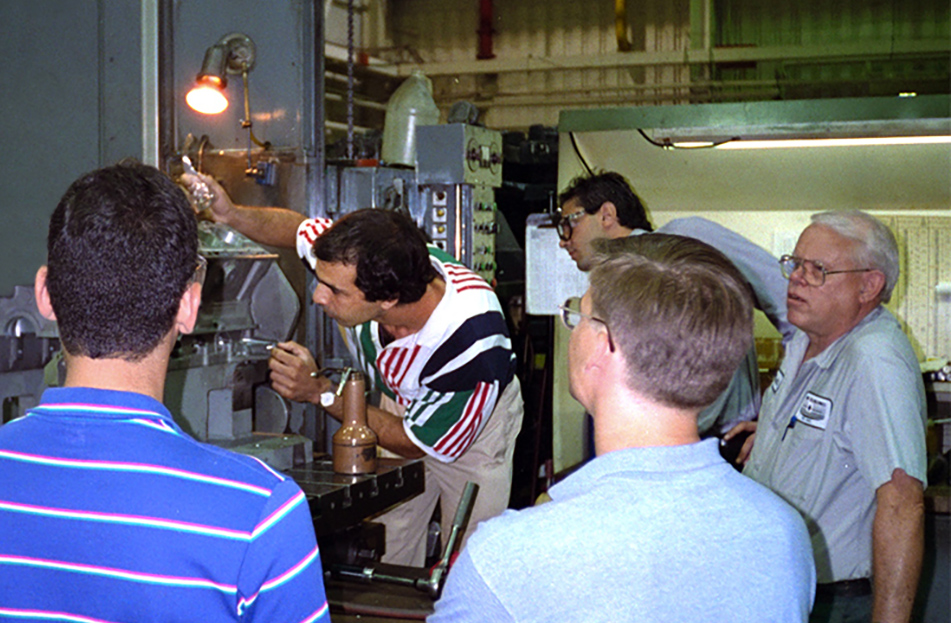
Members of the V12 team: Bernard Ibrahim, Anthony Musci, Don Nowland, Luis Cattani and John Hahn. Copyright Anthony Musci (used with permission).
Turning waste into energy
After Ford, Musci’s career spanned continents and a vast range of applications, from optical networking, electronic control systems and consulting …to burning industrial waste. The latter project brought Musci in contact with Michigan Metrology’s Don Cohen roughly 20 years ago to help solve some vexing problems. The particular project involved using large Stirling engines to burn non-hazardous waste from several industrial processes. The process safely disposed of the waste, while heat generated from the process could provide heat and energy for the facilities.
One issue the design team faced was getting a very large “swashplate” (which took the place of a crankshaft in a conventional configuration) to survive a low oil condition that would arise during some quick shutdowns. The engineers knew that surface roughness would be a major factor, though they were not certain which aspects of the texture would prove most critical. “it’s never just an Ra [average roughness] situation,” said Musci. Based on 3D optical profiler measurements from Michigan Metrology, they found that, in addition to the surface finish, the bearing area (Tp) and oil retention in the valleys was critical to control. Based on this 3D texture data, the team developed superfinishes on the swashplate and complementary finishes on the mating sliders which allowed the units to quickly shut down during low oil conditions with damage.
Heat…and speed
Another challenging issue that Musci helped address involved a high-speed gear box in a gas turbine application. “Most of the gear boxes were disintegrating in just a few hours,” said Musci. The gears faced tremendous loads at high speed. Musci recalls that the gears were undergoing over “75,000 teeth engagements per second—75 teeth engagements per millisecond!”
A combination of the right materials, heat treatment and surface finishes would be required to make gears that could survive such a brutal environment. To figure out that combination, “We’d design and build gear boxes, run them, and they’d either wear in and work, or wear out and fail.” They could then examine the best and worst surfaces to understand the characteristics of each both before running and if possible after running. “By using 3D measurement data instead of just popping out an Ra number, you could see what was going on, tweak the oil retention, and so on.” Michigan Metrology again provided 3D optical measurements—including samples of the surface of the small gears, and stitched measurements of larger areas to reveal the entire story of what was actually happening across the full engagement area of gear teeth. The team then used the surfaces of successful gears as the target for the next generation in development. After several rounds of optimization, they produced gear boxes that could run for “tens of thousands of hours” and billions of cycles. Advanced surface measurement, and the engineering savvy to draw the right conclusions from the data, was the right combination to solve the issue.
What’s next?
Today, Musci remains restless to explore new fields and apply his broad range of experiences to solve new problems. He is currently heading up engineering at a new venture for advanced 3D printing, among other active ventures. His deep understanding of materials and surface finishes, and his innate sense of how to apply them in many different applications, will no doubt lead to many more fascinating chapters in his career.
* Musci’s stint at Ford actually took place some years after the time period covered in the movie, but in similar environments.
- Musci, Anthony. “The Origins of Aston Martin’s V12,” Design Judges, March 16, 2020. https://www.designjudges.com/articles/the-origins-of-aston-martins-v12