In August 2024, Michigan Metrology will celebrate our 30th anniversary in surface roughness measurement. Over the next months we will be taking a few trips down memory lane to remember how we got here, and some of the adventures we’ve had along the way!
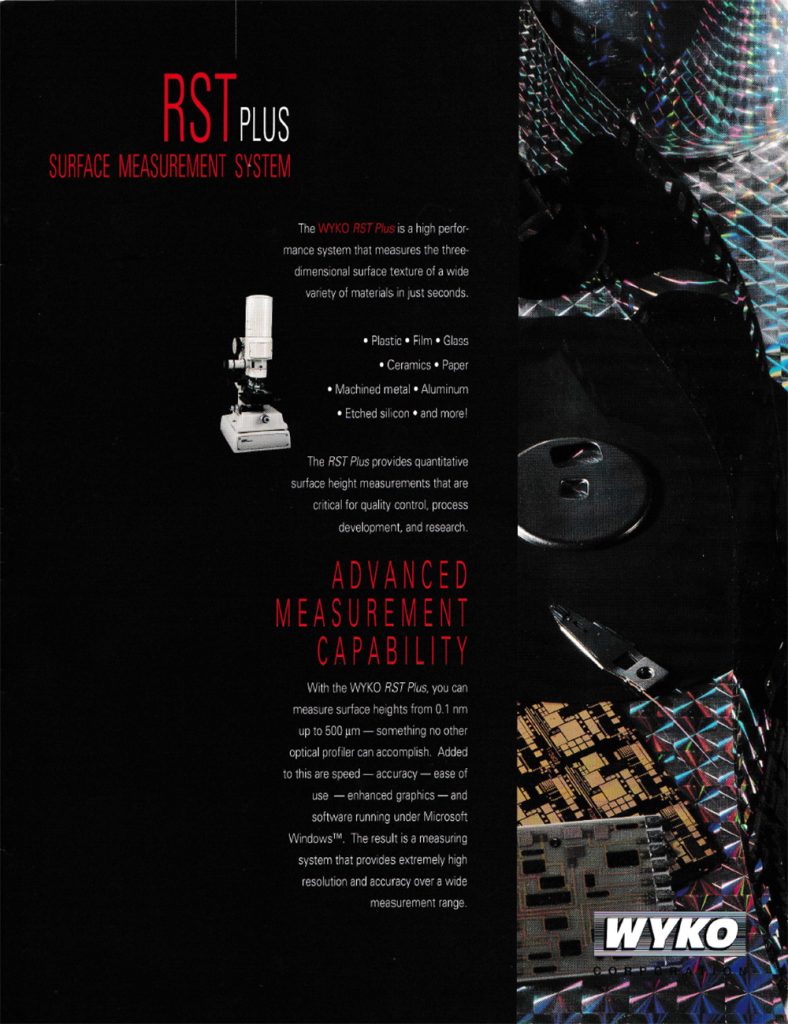
The WYKO RST Plus 3D Optical Profiler brochure, 1994
The brochure pictured above recently surfaced in a drawer in our office. The RST was one of the first 3D optical profilers to incorporate both white light interferometry and phase-shifting interferometry, to measure rougher surfaces with amazing (for the time!) resolution. I was fortunate enough to have worked with the team on its development, and some of its precursors, as an employee at WYKO Corporation in the late 80s and early 90s.
The early days of WYKO in Arizona were an amazing, frenetic, and fruitful time. Innovations were being developed at a crazy pace, driven by new measurement requirements for optics, disk drives, and other applications, and by the faster, more powerful computers that were hitting the market every day.
WYKO’s earliest instruments used “phase-shifting interferometry” to measure very smooth optical surfaces. I got to be a “fly on the wall” for a lot of the earliest development. I was working on optical disk drives at IBM, and I was also a grad student in Jim Wyant’s group, visiting him for my reviews in the early “strip mall” WYKO offices.
I officially joined the WYKO team in 1988. At that time, WYKO had started producing the TOPO 3D, 3D phase-shifting system. It represented a major advancement, offering “3D” measurement, though it was limited to measuring smooth surfaces. We knew that if we could develop a system that could measure rougher surfaces, we could introduce precision measurement to many new fields. I recall one of my coworkers had a freshly honed engine block in the back of his pickup. He dragged his fingernail along the bore and said, “This is what we need to measure.” Prophetic!
One of our first projects was developing an “autofocus” system. That team developed a method to scan the optical head vertically to find the best focus for a point—which we found we could do within a few nanometers! 1
A few years later, with some clever computing and engineering, the team developed a way to find the best focus for every pixel in the array, and to convert that information into a height map of the surface. “Vertical Scanning Interferometry” (VSI) was born.
The RST (and RST Plus) incorporated VSI as well as PSI, making it possible to accurately measure rough surfaces and small steps. We could now measure traditionally machined surfaces after processes like shot-peening, etching, etc. As a non-contact technology, the RST was also perfect for optics, disk drive components, semiconductors, MEMs, biological samples, and many other surfaces that could not be measured with a sharp stylus.
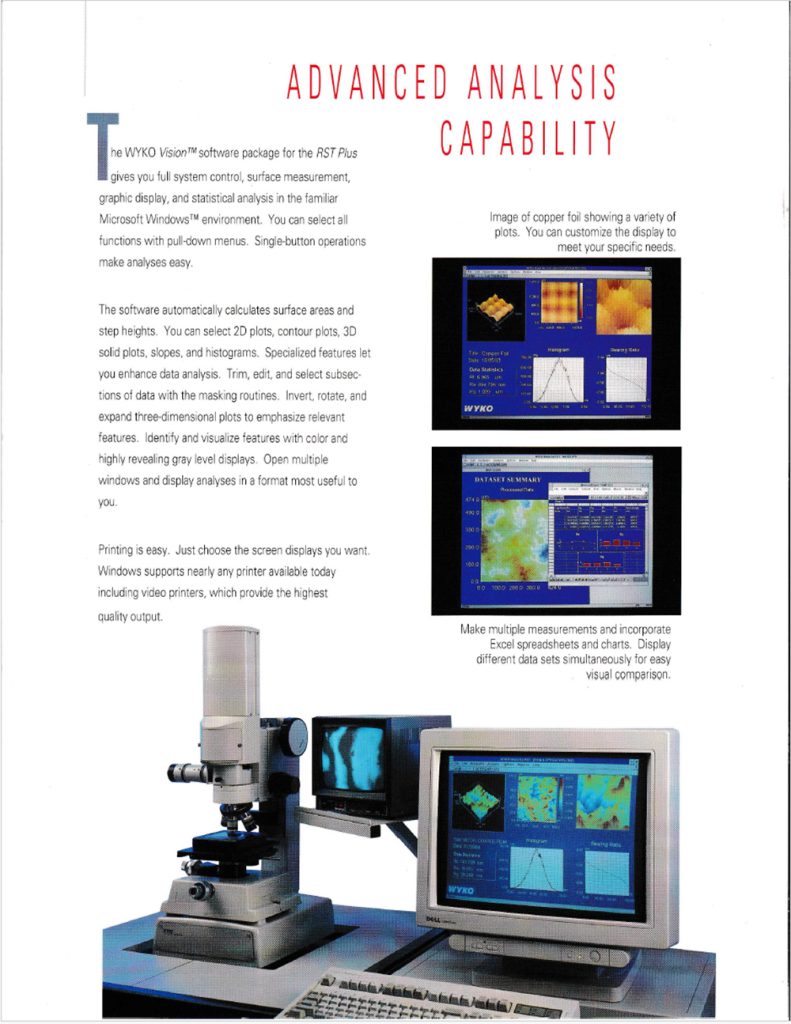
More from the RST Plus brochure, 1994.
As personal computers progressed, processing power became affordable and commonplace. The field of “3D optical profiling” matured rapidly. Measurement time decreased, scan range increased, and analysis capabilities grew to levels we had not fathomed just a few years earlier.
When I make measurements now with the powerful Bruker NPFlex in our office, I’m grateful to have been part of the team of engineers, scientists, machinists, and early adopters who helped make this technology a reality. I remember all of those animated conversations, late night development sessions, and scribbling on napkins that were the hallmarks of those early days. Those people made these amazing instruments—and Michigan Metrology—possible.
- Don Cohen
- Caber, P., Cohen, D. (1992). Effect of detector noise on the positioning accuracy of an autofocus system, Applied Optics, Vol. 31, No. 31, 6684.