Rotary lip seals create a boundary around shafts in rotary equipment, typically to retain lubricant on one side versus air or gas on the other. On first consideration, it would make sense that a seal would act as a barrier, holding back all lubrication. In reality, however, when a sealing interface is working optimally, fluid is moving under the seal, but it is also moving back again, with none lost over time.
The sealing interface can be thought of as two pumps. The first pump is the seal itself. As the seal acts on the shaft, microasperities in the sealing surface can form a pattern that acts like a series of hydrodynamic wedges that pump the fluid, typically in one direction of motion only. In many cases a seal will have more than one lip in order to address different directions of rotation.
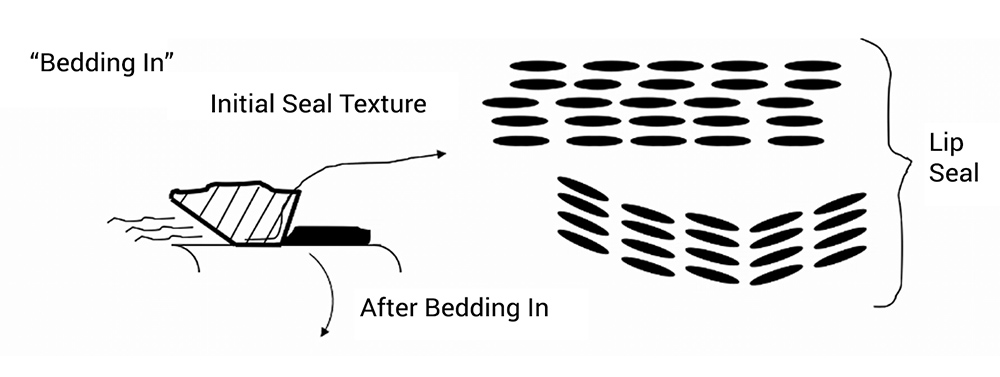
Micro-asperities become oriented and act like hydrodynamic wedges which help lift the seal and pump fluid into, and then out of, the interface
The second pump is the shaft. “Lead” on a shaft refers to tooling marks from turning operations that survive grinding and polishing. Lead can cause the shaft to act like a screw pump, driving fluid through the seal or drawing it away from the interface. The “lead angle” will dictate the degree of pumping that takes place.
Much research has gone into measuring and controlling lead, which we may refer to as “macro lead,” the kind we can see, measure, and fix. But this is not the entire story. A second phenomenon, which we might call “micro lead,” occurs on the scale of surface roughness. In micro lead, pockets in the surface texture can carry fluid into or out of the interface. The effect of any individual pocket is small, but cumulatively they can have a significant bearing on seal performance.
Micro-lead is more challenging to detect and measure. It often only becomes an apparent cause when a seal is leaking, after all “macro” considerations have been ruled out. To measure micro-lead we can examine the surface texture and build up a histogram of the sizes and directionality of the pockets. If the pockets are equally distributed, the seal should perform well. If the pockets are biased in one direction or the other, the surface texture may cause the surface to pump liquid.
Some interesting work has been done on this topic, including work by Matthias Baumann (www.ima.uni-stuttgart.de).
To learn more about seals, and the effects of surface texture on sealing, check out the Sealing module from our Surface Texture and Tribology short course, available through udemy.com.