Key concepts in tribology have often been discovered by trial and error…then made more broadly useful through rigorous work that uncovers the broader understanding.
Such is the case of material compatibility. Ernest Rabinowicz went to great lengths to understand the relationship between material properties and wear, to determine the characteristics that work best in sliding friction applications.
Rabinowicz’s work on metals
The table below, from his book Friction and Wear of Materials, summarizes this work. The basic principle that Rabinowicz’s work reinforced is that incompatible materials work best for sliding interfaces such as bearings and bushings. Compatible materials are prone to localized bonding and welding, which increase the coefficient of friction and lead to premature wear at the interface.
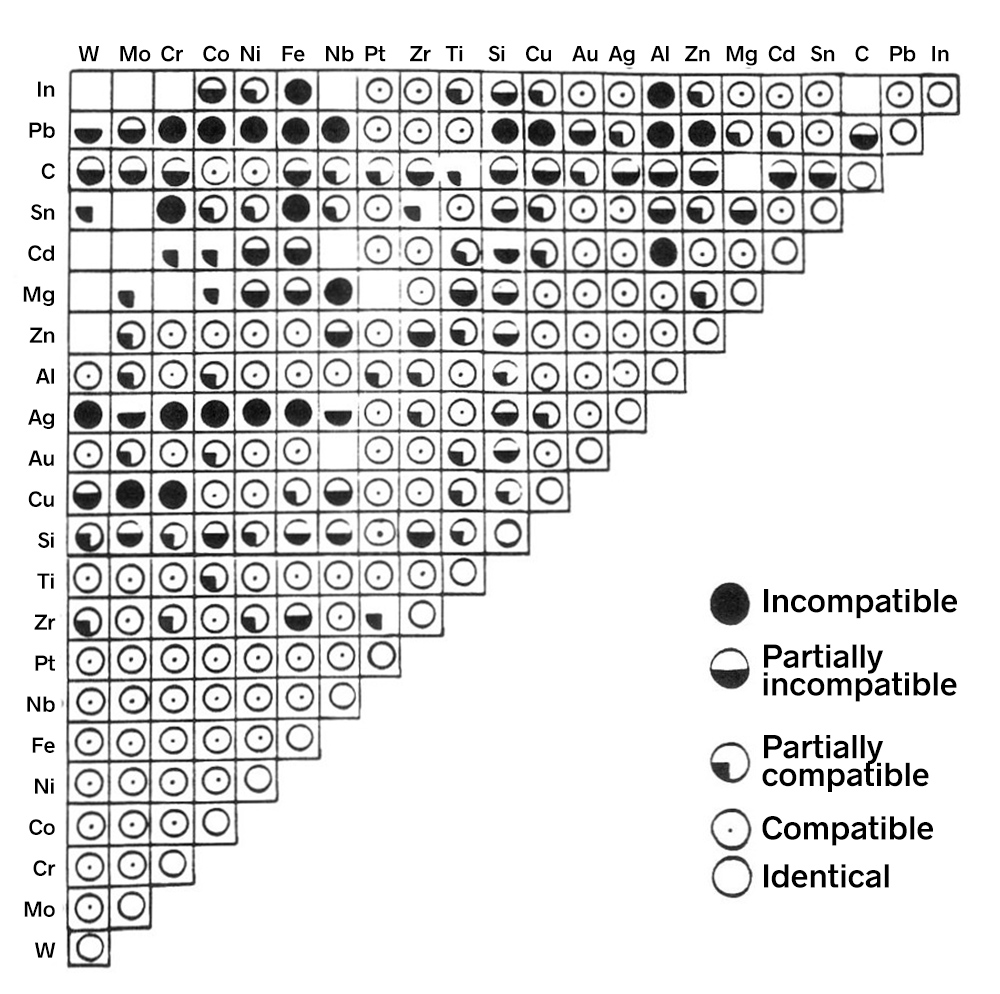
One interesting discovery he noted is that certain crystal structures result in a lower coefficient of friction. Metals that bond in an HCP (hexagonal closest packed) structure, such as hexagonal cadmium cobalt, interacted the least with mating materials and were therefore best for sliding surfaces.
Caveats—and lots of them
Rabinowicz’s chart, which was the most comprehensive at the time, unfortunately only extends to metals. As Rabinowicz, and many others, have determined, the exceptions sometimes seem to outnumber those that follow the general rule.
- Diamond Like Coatings. By the rule above, two surfaces with similar coatings ought to perform poorly in dry, sliding applications. Yet, two surfaces with diamond-like coatings will slide against each with a very low coefficient of friction.
- Polymers. For polymer-on-metal and polymer-on-polymer interfaces, the story is much more complicated. Take PTFE, a common bearing material chosen for its low shear strength. In order for the coating to perform correctly, PTFE needs to transfer from one side of the interface to the other. Once this is accomplished, the actual shearing at the interface takes place between PTFE and PTFE. The challenge, however, is in retaining PTFE in the interface: the same low sheer strength which makes it good as a bearing surface is precisely what makes it hard to keep in place.
- Lubrication. Rabinowicz’s chart only describes dry sliding interfaces. The goal in lubricated interfaces is to retain a film of lubrication to separate the bearing surfaces. In lubricated applications, we still must choose the proper bearing materials, but we also need to develop the correct surface texture to retain the lubricant but also enable the lubricant to sheer. To do so, we need to control both the surface texture and the surface energy so that the lubricant remains bonded to the surfaces yet freely sheers as well.
In short, the work begun by Rabinowicz and other continues to this day. Our understanding of the materials and surface texture that produce good bearing interfaces is constantly growing and changing. You can learn more in the Dry Sliding Friction and Lubricated Friction modules of our Surface Roughness, Texture and Tribology short course, available on udemy.com.