Cavitation is the formation of air bubbles in a fluid as it goes from high pressure to low pressure. The dissolved gas can grow into bubbles—and under certain conditions those bubbles can implode, with force. We most frequently hear about cavitation in relation to propellors and impellers, where it can reduce performance or lead to excessive noise and wear.
The video below (thank you to Matevz Dular) shows a single cavitation bubble collapsing and the damage that the single burst can cause.
But cavitation is not confined to propellors: it occurs in other components as well, particularly in systems in which fluid is maintained at both high and low pressure. In these systems, fluid can leak under or around seals, carrying trapped air with it. Under normal operation, the air in the thin layer of leaked fluid can exit the interface through the same gaps that it entered, without issue, as shown below.
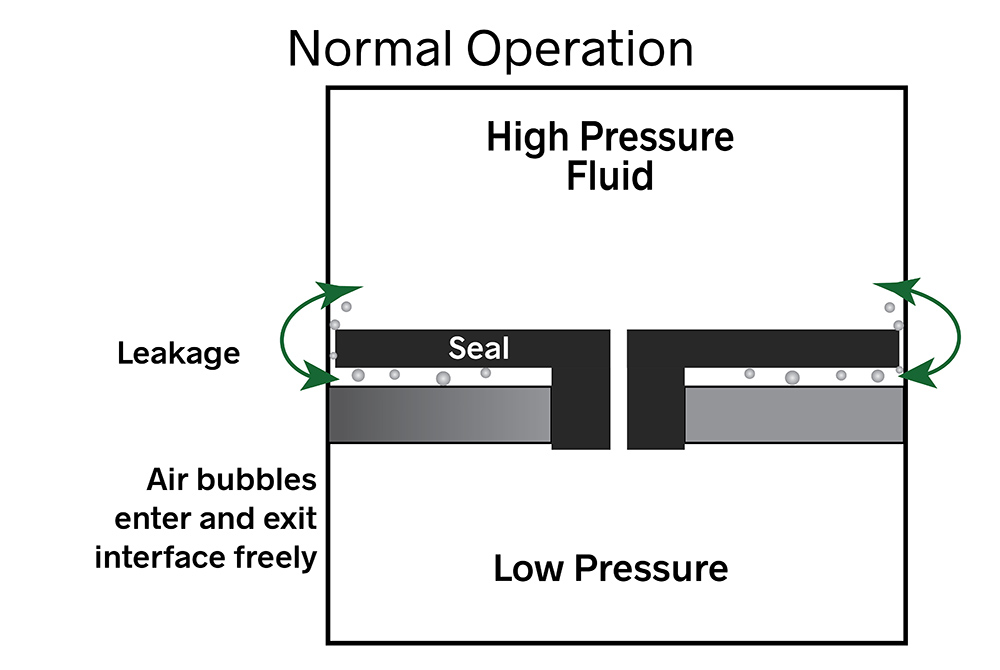
However, if the interface is subject to sudden, extreme shocks, then the trapped air bubbles cannot escape quickly enough. Instead, they implode, ejecting streams of air that are energetic enough to wear away the surface—even hard surfaces such as steel. This ongoing erosion can lead to significant material removal—even hundreds of microns in depth—that can rapidly degrade the component.
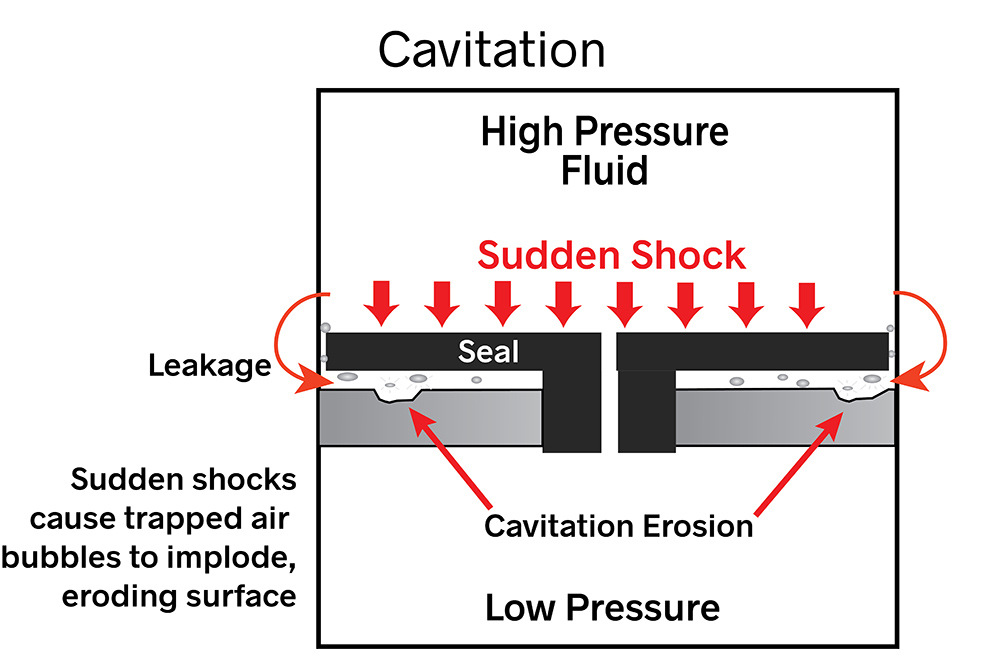
The 3D surface data shown below is from a high-pressure component that failed very quickly after entering service. The manufacturer came to us to help determine the wear mechanism(s) so that corrective measures could be taken. The wear caused a large step in the surface, and the worn area was shiny (i.e., the short wavelength surface texture had been worn away). Both of these aspects suggested an erosive wear process, rather than abrasive or adhesive wear. The round “valley” areas were much like those created by a “peening” operation, leading us to conclude that cavitation was the primary wear mechanism.
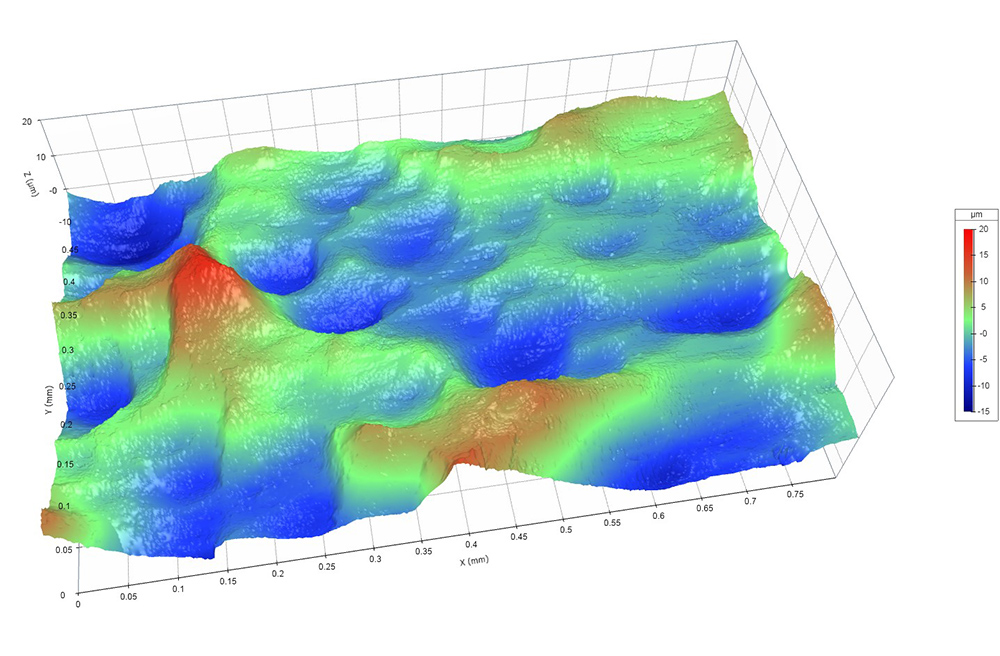
Any system with fluid and particles (i.e., bubble nucleation sites) can be subject to cavitation, including pumps and food processing equipment. The good news is that, quite often, the problem can be solved by simply heating the operating fluid before it is introduced into the sealed system. Heating the fluid drives out any air bubbles, thereby removing the possibility of cavitation from the start.
If you’d like to know more about cavitation, or if you’re trying to diagnose any kind of wear issue, contact us for more discussion.