Ssc
Ssc is the Mean Summit Curvature for the various peak structures. Peaks are found as described above for the summit density. Ssc is given by the following:
Note that Ssc is not strictly defined in the ISO 25178-2 but was established earlier in the research which contributed to ISO 25178-2. Future sections of ISO 25178-2 may address parameters such as Sds as “Feature Parameters”.
It is first evaluated for each summit, then averaged over the entire area.
Real Area of Contact
To understand how the surfaces interact, we need to understand the “real area of contact” between the two surfaces. When surfaces are in contact not all points are in contact:
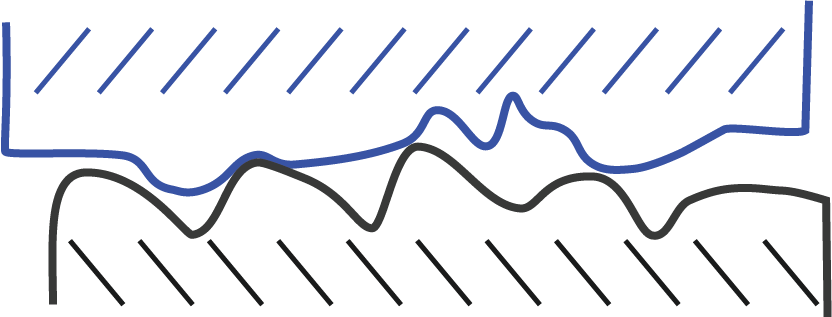
Therefore, we need parameters that can describe how much of the surfaces actually are touching, and the shape of those areas that are making contact. Ssc (the Mean Summit Curvature) which is an indicator of the shape and size of the higher areas of a surface. It is often used in conjunction with Sds (the Summit Density), which counts the number of summits per unit area of the surface.
Shot Peened Surface. Ssc = 37 mm-1 (i.e., mean radius of curvature is 27 µm.)
Application
Ssc and Sds are useful in predicting the degree of elastic and plastic deformation of a surface under different loading conditions and thus may be used in predicting friction, wear and real area of contact for thermal/electrical applications.
Ssc provides a sense of the size of the peaks. A large Ssc indicates small, needle-like summits, which will provide a smaller area of contact and possibly lower friction (assuming elastic deformation). These structures, however, may not be sturdy and may crush (i.e., plastically deform) during initial contact, resulting in some degree of wear, and higher friction after a period of contact.
If the Ssc is high (i.e., small radii) and the material is hard, the sample may abrade/cut a softer mating surface, again leading to higher friction and wear.
A small Ssc indicates structures with larger radii, which can support the contact load elastically. Think of a field of mushrooms as a surface with a small Ssc.
The application dictates the Ssc value that is required for optimal function. For an electrical contact, for example, we may want a surface with a high Ssc, predominated by spikes that can penetrate the oxide layer which may build up over time. A low Ssc surface may provide better long term wear on parts that undergo large loading forces.
This surface includes summit structures which would most likely make contact and support a load with a mating surface.
For more information on Ssc, see the blog article, Using Ssc and Sds to understand how surfaces interact and wear.
Read about Sds and Ssc as they relate to medical devices in the blog article, What surface finish does a medical device need?