In this 3-part series we look at the case of dry, sliding friction and discuss how surface roughness and materials impact the surface as a bearing.
PART 1. Real area of contact
As a general rule, for a bearing surface that will undergo dry sliding, we want to achieve the lowest possible friction. Several factors go into reducing friction, including materials and surface roughness. Let’s start by talking about roughness.
When we plot friction against roughness, we often get a curve with a “bathtub” shape, as in the plot below. Friction is very high for very smooth surfaces (left), dropping to a minimum, then rising again when the surfaces are very rough (right).
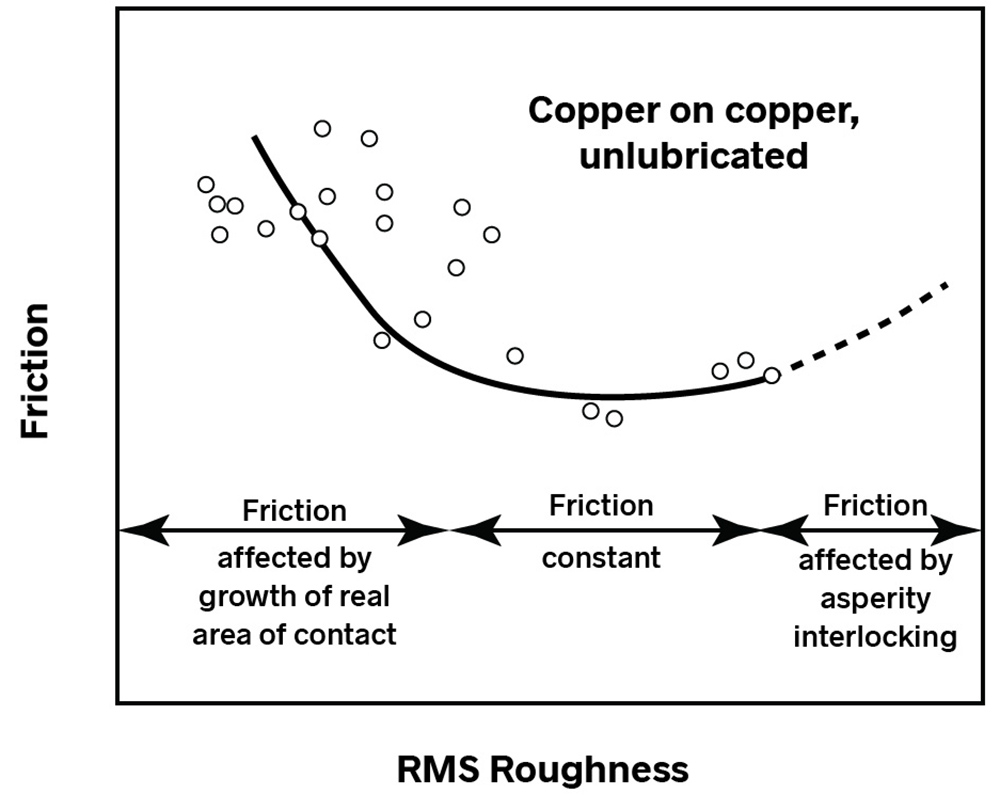
These three examples represent the portions of that bathtub curve.
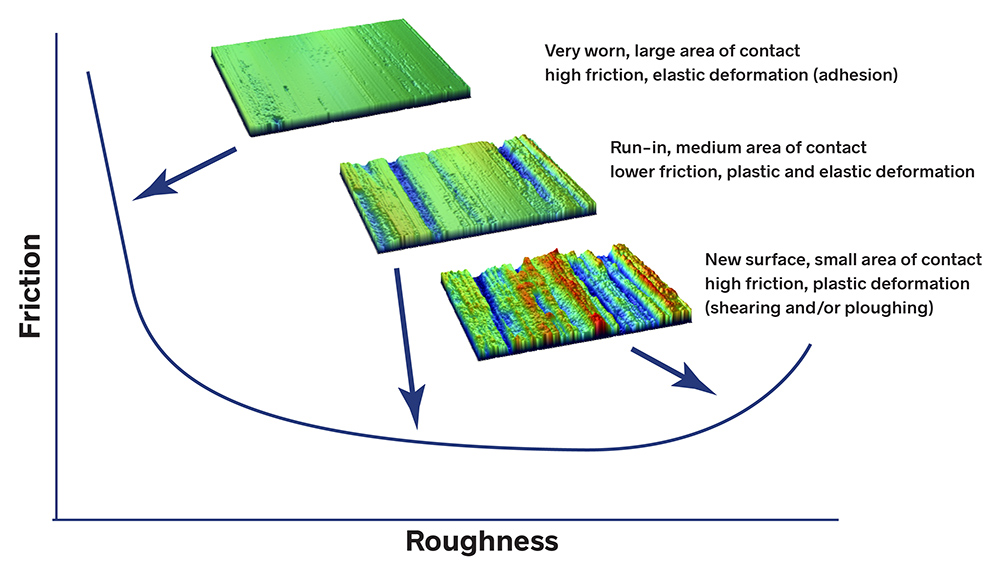
In the top 3D map, the surface is very smooth. As we discussed in our Real Area of Contact blog post, friction increases with the “real area of contact,” the microscopic portions of two surfaces that are supporting the load. For very smooth surfaces, the real area of contact is high (assuming elastic contact), and the coefficient of friction is high. The surface may tend to adhere, or even locally weld or gall.
The surface in the bottom map is very rough, with the load being supported by many tall, thin summits. Here, the friction is also high—but in this case, a large real area of contact is not necessarily the cause. In this case, high friction is due to the shearing and plastic deformation of the peak material, or ploughing of the peaks into the other material in the interface.
The middle example shows a surface in which the load is supported by a number of large, somewhat smooth peak areas (summits). This is the type of surface we might expect to see after a component has been used for a period (i.e., after it has been “run in”). This is surface texture is good for a bearing because it provides a small area of contact for low friction, yet sufficient material to provide durability. The texture also provides void space to capture debris and remove it from the interface.
In next week’s post we will look at material properties that can lead to good bearing surfaces. In two weeks we’ll wrap up the series by bringing it all together in a discussion of plasticity.
References:
- Ernest Rabinowicz, Friction and Wear of Materials, John Wiley & Sons, 1995.
- Frank Philip Bowden and David Tabor, Friction, An Introduction to Tribology, Robert E. Krieger Publishing Co. Malabar, Florida 1973.
- Greenwood, J. A. and Williamson, J.B.P (1966), “Contact of Nominally Flat Surfaces”, Proc.Roy.Soc Lond. A295, 300-319.
- Bharat Bhushan, Introduction to Tribology. John Wiley & Sons Ltd, New York, 2013.
Please fill out the form below to download this article as a PDF: